共计 1674 个字符,预计需要花费 5 分钟才能阅读完成。
总觉得出了问题就“开个培训”能解决;
讲几遍“不良率高了是因为你没按作业指导书”,就能让车间师傅顿悟。
但现实呢? 讲了也白讲、贴了也不看、写了也不执行。你说质量意识怎么就这么难管?
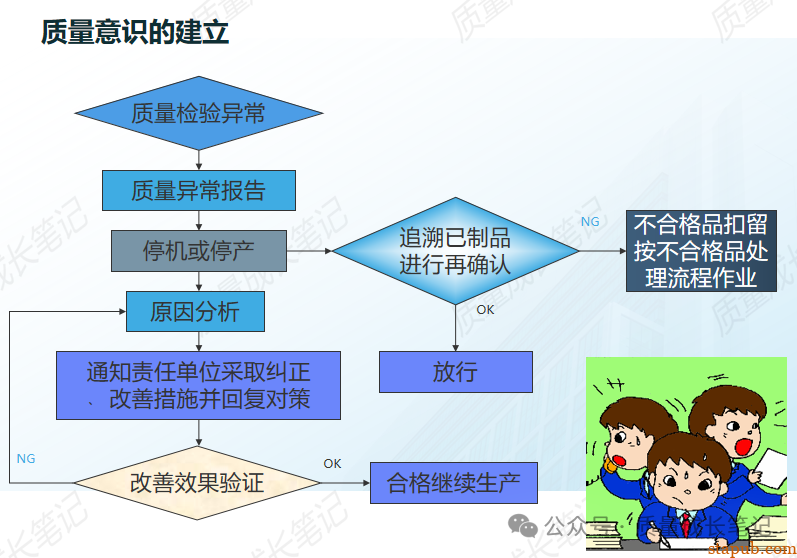
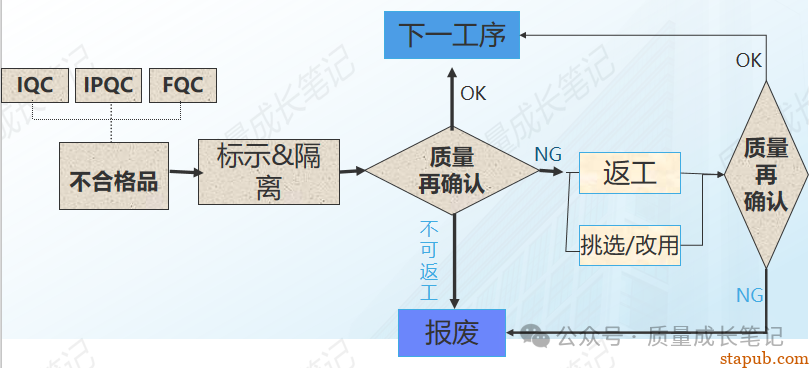
一、什么是“质量意识”?
打个简单的比方:有没有把“做出好东西”当回事,决定你有没有质量意识。
专业点说,质量意识是指员工对质量管理的理解、重视程度,以及在实际工作中主动维护和提升质量的意识和行为习惯。
它不只是懂标准、背流程,而是体现在:
-
出问题后第一反应是“怎么改善”而不是“找借口” -
工作中不做多余事,但也不会少做关键事 -
对质量问题有“过敏反应”,不是“这次放过去吧”
质量意识的终极形态:全员、全过程、全方位参与质量管理。而不是出事找质量,平时不关我事。
二、质量意识难管的根源
说白了,大多数企业提升质量意识,常常踩进以下几个“坑”:
1. 把质量当“质量部”的事
很多员工压根没觉得自己该对质量负责——
-
操作员觉得:我按图做了,问题你去找工艺部 -
工艺员觉得:流程我给了,是你检验不严 -
检验员说:我出报告了,是你放行的 -
最后质量部全兜着,还得被客户骂、上级喷
质量不是一个部门的事,是整个流程的事!只有大家都动起来,质量才不是一个人在那里着急上火。
2. 只看结果,不管过程
很多人对质量的认知还停留在“出厂合格就行”。
但大家都知道,一个产品合不合格,不是最后检验决定的,而是从前道工序开始,一环扣一环影响的。
只盯着终检,就像医生只看病人死没死,不管中间吃了什么药、动了什么刀,那还怎么防错?
3. 把质量文件当“应付审核”的
SOP挂在墙上,没人看; SIP写得很好,没人执行; 巡检表天天打勾,出了问题连数都对不上……
文档不是摆设,而是“操作依据”—— 员工看不懂、不愿用、不习惯,都是质量意识不强的体现。
4. 达标就万事大吉,没“持续改进”概念
“反正客户没投诉,能出货就行。”
但问题来了—— 客户对你失望也是有个过程的:你今天只是“几处不满意”,明天就是“取消下单”。
持续改进不是口号,是企业能不能持续生存的底线。
5. 问题都甩锅,没人反思自己
“模具有问题怪设备部”“材料变形怪采购”…… 反正永远不是自己的问题。
但如果质量人也默认这种甩锅文化,那就不是在推动改进,而是在维稳。久而久之,团队的质量意识只会更差。
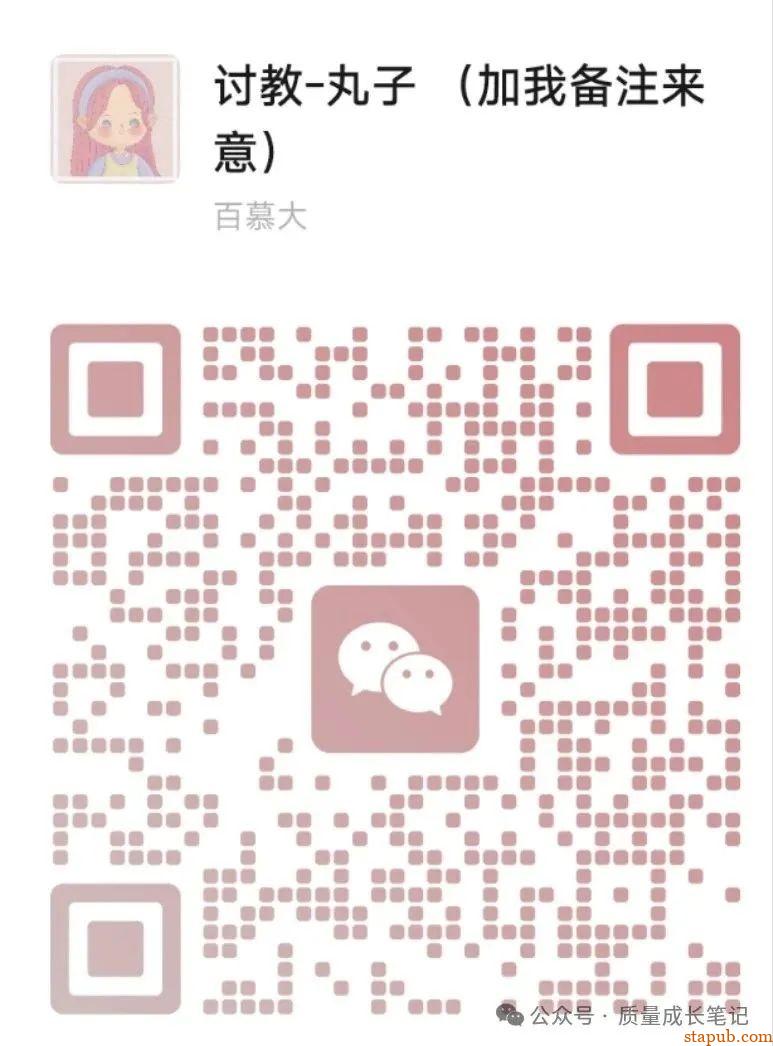
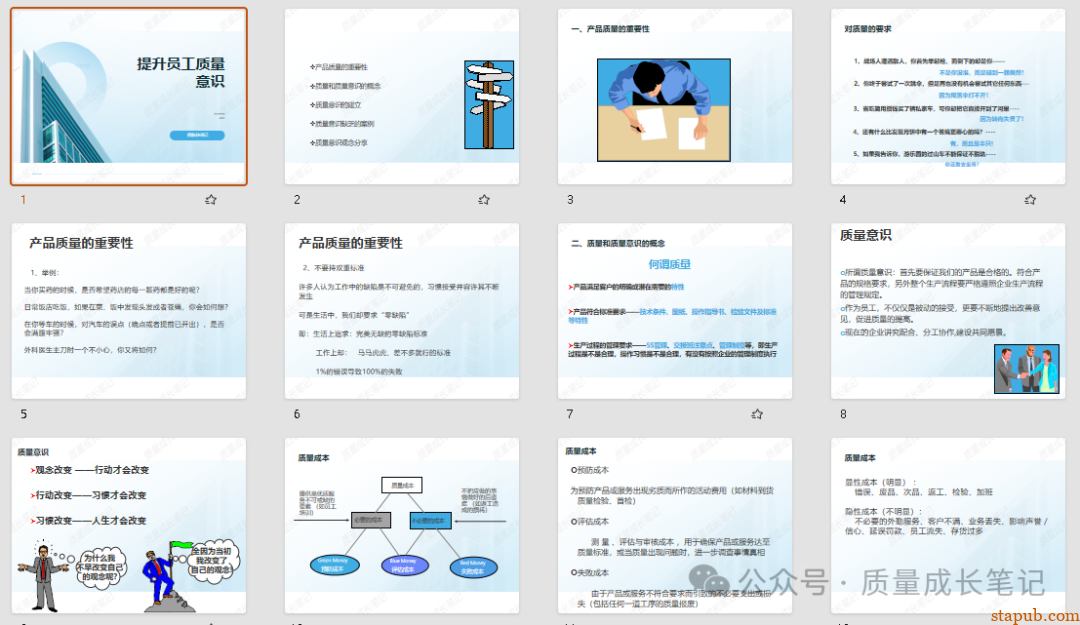
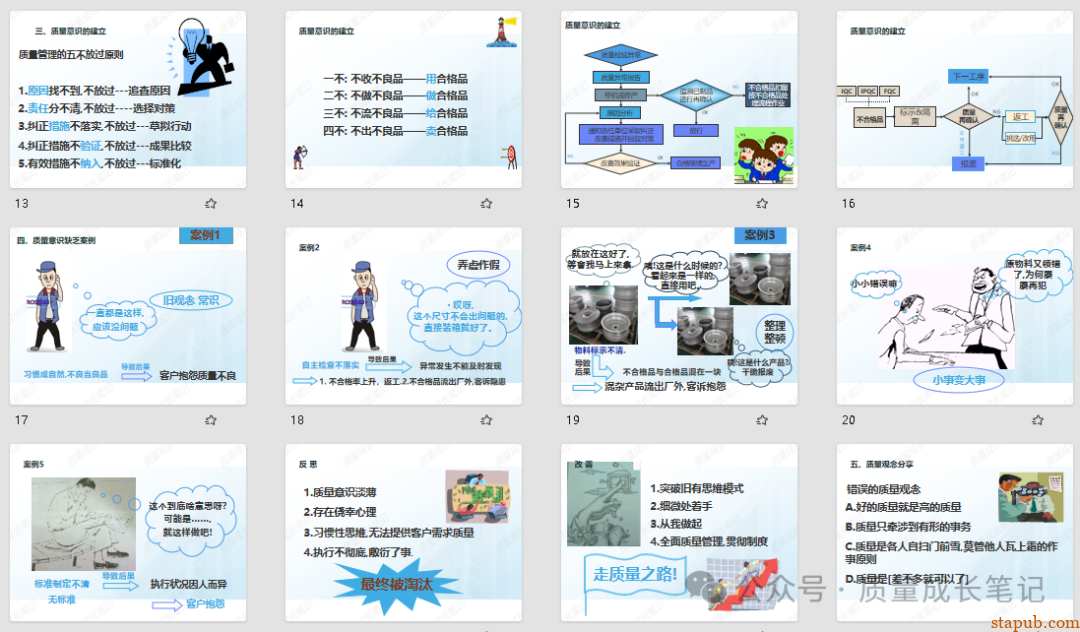
三、怎么才能管住质量意识?
好消息是,质量意识不是天生的,是可以培养、塑造的。但得讲方法。
1. 培训不能只讲“知识”,要讲“意识”
知识是能考过的,意识是能做对的。
所以培训要结合实际案例讲:
-
不按标准操作出过啥问题? -
为什么看似不重要的参数最后引发了客户抱怨? -
“差不多”到底多差?
让员工知道不是“你麻烦”,而是“你负责”。
2. 搭好激励机制,让质量行为“值钱”
比如:
-
设立“质量改善奖”,奖励提出合理建议的员工; -
对反复犯错但不改进的岗位挂“红榜”,拉通报; -
在绩效里加入“质量行为分”,让“做得好”看得见。
质量意识不是靠讲出来的,是被“引导”出来的。
3. 把流程责任拆清楚,谁负责哪一段写清楚
让每个岗位都明白: 你不是“看完文件就好”,你是对这一段质量负责。
设计:你保证设计输出的合理性 工艺:你保证参数设定的可执行性 操作员:你负责按SOP执行 质检:你负责过程控制与反馈闭环
责任清晰,才能让质量变成主动意识,而不是被逼着做。
4. 用数据说话,让问题变“看得见”
-
一线可视化看板显示不良率变化趋势 -
各工序质量指标进行横向对比排名 -
每月质量事故做定量复盘+行为纠偏
质量问题不能只停留在口头通报,要让数据说话,让现场看到“我做错了”和“别人做对了”的区别。
5. 让质量成为“文化”而不是“压力”
质量意识不等于天天抓不良、天天追责任,而是:
-
帮员工看见“做好”比“做完”更有意义 -
帮管理层认识“质量问题”是系统问题,不是单点问题 -
营造一个敢说问题、能改问题的环境
你不需要一个背锅的质量部,你需要一支“全员质量人”的团队。
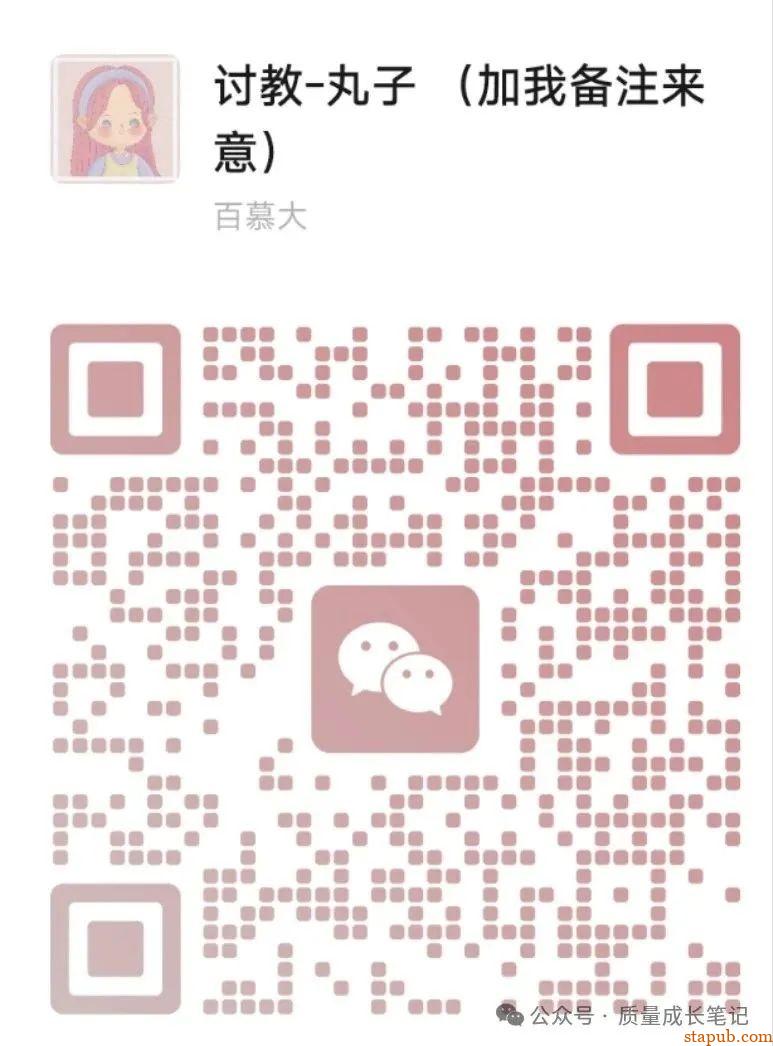
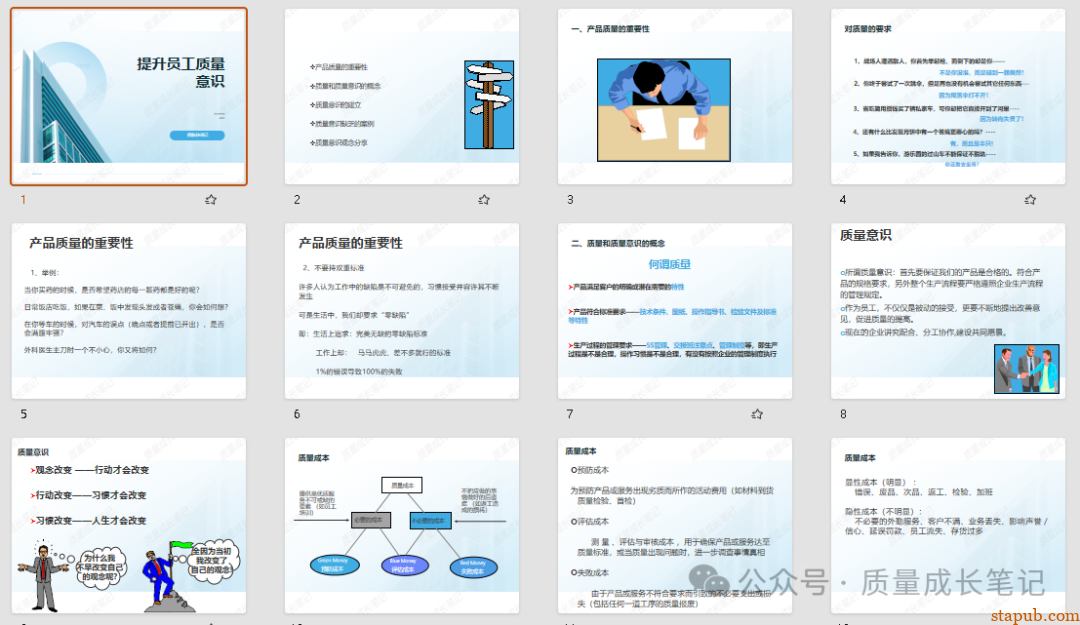
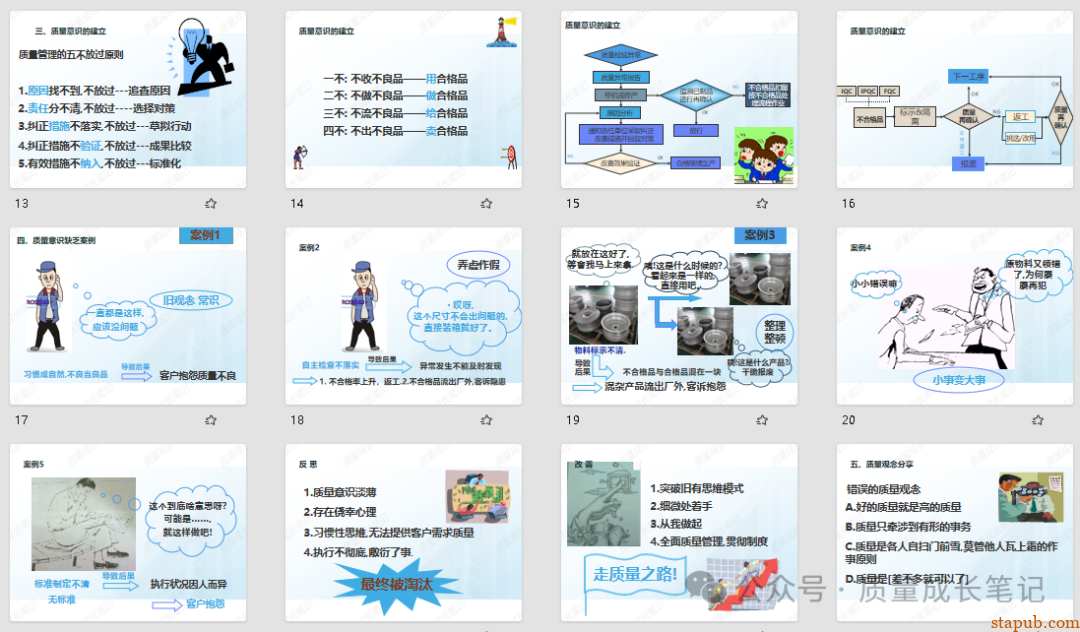
最后说一句:
质量意识确实难管,
但它不是不能管——只是不能靠喊口号去管。