共计 1314 个字符,预计需要花费 4 分钟才能阅读完成。
1.渗碳
目的: 向低碳钢或低碳合金钢零件的表面层渗入碳原子,提高表面的含碳量。
原理: 将零件置于富碳介质(气体如丙烷/天然气、固体如木炭+碳酸盐、液体如熔融氰盐)中,加热到奥氏体化温度以上(通常 900-950°C)。碳原子在高温下分解并扩散进入钢的表面。
后续处理: 渗碳后,零件需要进行淬火处理,使高碳的表面层转变为高硬度的马氏体组织,而低碳的心部保持强韧性。
特点:
①可获得较深的硬化层(通常0.5mm – 2mm甚至更深)。
②表面硬度高(HRC 58-65)。
③主要用于承受较大接触应力和磨损的零件,如齿轮、轴、凸轮、销轴等。
④处理温度高,零件变形相对较大。
⑤材料要求:必须是低碳钢或低碳合金钢(含碳量一般低于0.25%)。
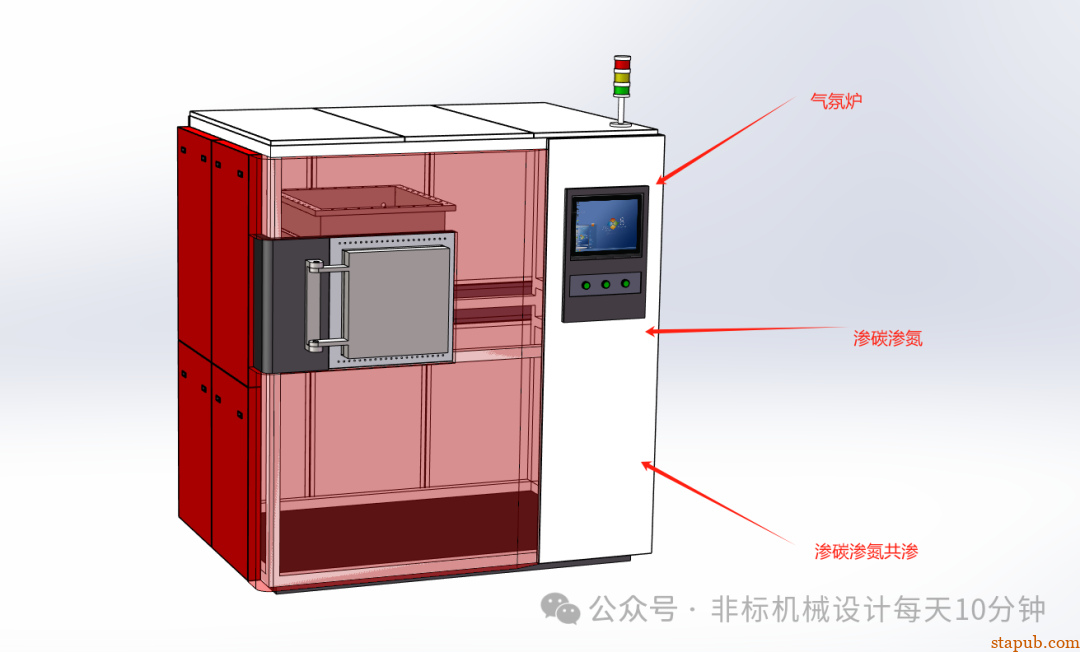
2.渗氮
目的: 向零件(通常是含Cr、Mo、V、Al等合金元素的特殊钢,如38CrMoAlA,或某些不锈钢、工具钢)的表面层渗入氮原子,形成高硬度的氮化物。
原理: 将零件置于含氮介质(最常用的是氨气)中,加热到铁素体或奥氏体状态下的相对低温(通常 500-580°C)。氨气分解产生活性氮原子,扩散进入钢的表面,与合金元素形成细小、弥散分布的硬质氮化物(如AlN, CrN, VN, MoN)。
后续处理: 不需要淬火。渗氮过程本身就在较低温度下形成了高硬度的化合物层和扩散层。
特点:
①可获得极高的表面硬度(HV 1000-1200甚至更高,相当于HRC 68以上)。
②硬化层较浅(通常0.1mm – 0.6mm)。
③处理温度低,零件变形极小,适用于精密件。
④表面形成的化合物层具有优异的耐磨性、抗咬合性和一定的耐腐蚀性。
⑤显著提高疲劳强度。
⑥主要用于要求高硬度、高耐磨、高疲劳强度且变形要求严格的精密零件,如精密齿轮、曲轴、凸轮轴、模具、量具、缸套等。
材料要求:需要含有强氮化物形成元素(Al, Cr, Mo, V等)的专用渗氮钢效果最佳。
3.碳氮共渗
目的: 同时向零件表面层渗入碳原子和氮原子。
原理:
中温气体碳氮共渗: 最常用。在含有渗碳气体(如天然气、丙烷)和渗氮气体(氨气)的混合气氛中,加热到略低于渗碳的温度(通常 820-880°C)。碳和氮原子同时渗入钢的表面奥氏体中。后续需要淬火。
低温碳氮共渗: 有时也称为软氮化或氮碳共渗。在含碳氮的盐浴或气氛中,在渗氮温度范围(500-580°C)进行。主要形成以氮为主的化合物层(ε相),并伴随少量碳的渗入。不需要淬火(或仅需快冷)。
特点:
相比渗碳:处理温度较低,零件变形较小,淬透性更好(氮的作用),耐磨性更好,具有更好的抗回火软化能力。
相比渗氮:处理时间相对较短(尤其指中温共渗),可以获得比渗氮稍深的硬化层(中温共渗可达0.2-0.8mm),对材料要求不像渗氮那么严格(普通渗碳钢也可进行)。
结合了渗碳和渗氮的部分优点:
中温碳氮共渗后需淬火。
表面硬度介于渗碳和渗氮之间(HRC 58-63)。
应用广泛,适用于承受中等载荷、要求较高耐磨性和一定抗疲劳性能,且对变形有一定要求的零件,如汽车、拖拉机上的齿轮、轴类零件等。