共计 1564 个字符,预计需要花费 4 分钟才能阅读完成。
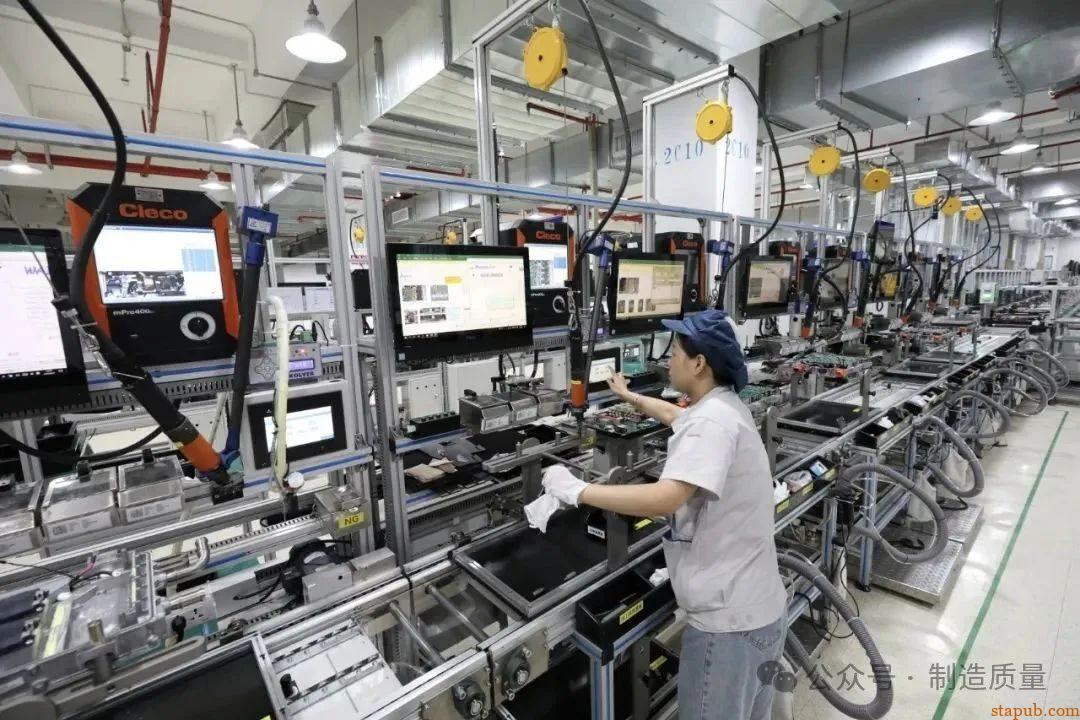
1. 漏工序的原因:
操作者方面,为了追求效率而忽略品质、新人或新岗位出现的不熟练、注意力不集中等。
管理方面,没有提供合适的方法以避免问题的出现,没有对操作者的操作方法进行调查,并提出合理的改进以提高效率等。
2. 漏工序检出难易度分类:
a. 困难(如攻牙、压披锋、刻印、涂漆)、
b. 中等(如冲小孔、折矮短边、铆接小件)、
c. 容易(如冲大孔,折长高边、铆钉、铆接大件)。
重点管控检出困难的工序。
3. 工序调机品管理:
工序调机合格后交付生产前,由调机人员将工作台面进行清理,将调机工具收纳归位,清理废料。
重点:将不合格品放入不合格品箱、将未能确认品质状况的产品放入待处理品箱,并交给QC确认品质状态。
模夹具异常后再次调机时,仍需按此要求执行。
由QC首检人员检查此规定的实施情况,并作为签单生产的标准之一。
4. 作业中断管理:
一切在正常连续生产时半成品可能停留的地方。如冲床、攻牙机、铆钉机、模具、夹具、拉线、包装台上。
当临近工间休息或下班时,对于单工序生产的,必须完成本工序;对于连线生产的,必须完成拉线上所有半成品。
任何本工序未完成品及完成品,只能出现在相应的已标识的胶箱中。
生产组长在工间休息或下班时,需检查责任区内此规定的实施情况,并负间接责任。
5. 离岗许可制:
在非工间休息时,操作人员需处理个人紧急事务的,必须向组长提出离岗申请并得到批准。
离岗前必须按作业中断管理的要求完成相关工作,并由组长确认相符后,方可离开岗位。
组长尤其要注意连线生产中员工的离岗要求及管理工作。
6. 物料分隔管理:
对于冲压和攻牙工序,一定不能放于模具/夹具与操作者的中间地带。
对于小产品,
1)未加工品和已加工品分别放置于操作者的两侧。
物料箱不能放于机台上的,需提出胶箱放置架的形式、大小和数量,并确定完成日期。
2)将未加工品和已加工品分别装入小胶箱中,做“未完成品”和“已完成品”标识,并放于冲床/攻牙机工作台面的两侧。
改进码模方式:没有气顶要求的模具,码模位置优先选码中间共两个,后选右后和左前方向共两个,方便将小胶箱放于右侧装未加工品;同时物料进出模具或夹具时操作方便,以及减少可能的刮花。
以上两点要求无法实施的,由组长提出模具/夹具/工具的改造方法和完成期限,由其直接上司负责跟进实施进度。
7. 非流水线包装漏工序:
包装组一般完成:全检、涂漆、擦拭、装箱等。漏涂或少涂是最常发生的。
对于漏涂问题,需用合适的胶箱分装不同半成品;对于少涂问题,如果涂的范围大,可以考虑分工序涂不同的范围。
从人角度考虑,包装组是相较于冲压攻牙在注意力方面最不集中的一个群体,根源是聊天、其他岗位串岗。
其岗位坐姿作业、比冲压工作安全,必须根除聊天现象,尤其是相邻工位的聊天。
8. 箱中首件检查:
为避免整箱半成品漏工序,每次开始生产一箱半成品时,操作者必须将箱中产品作首件检查,确定前一工序是否漏加工。
考虑操作者的可检查性:有无文件支持/是否了解前一工序的加工完成状态?
9. 间接人员造成:
非直接生产人员在生产线接触半成品时,可能因没有回位到相应机台,造成漏工序。
需控制非直接生产人员接触半成品的人数,培训需接触半成品的人员以提高他们的品质风险意识。
10. 半成品标识:
需要完善半成品标识管理。
对于制程不良后作为不合格品进行标识的半成品,有潜在漏工序风险,需完善不合格品处理流程。
指示清楚处理方式、处理方法、使用什么工具检验方法和工具、实施进度和效果确认。
11. 作业依据:
需要将相应的工序图/作业指导书悬挂于机台边,还需考虑机台边文件架的便利使用性。
12. 制程和客诉不良调查:
操作者为了追求效率而忽略了品质。如果说绩效考核是正向刺激,那么不良品出现之后的原因调查和追责就是反向制约。
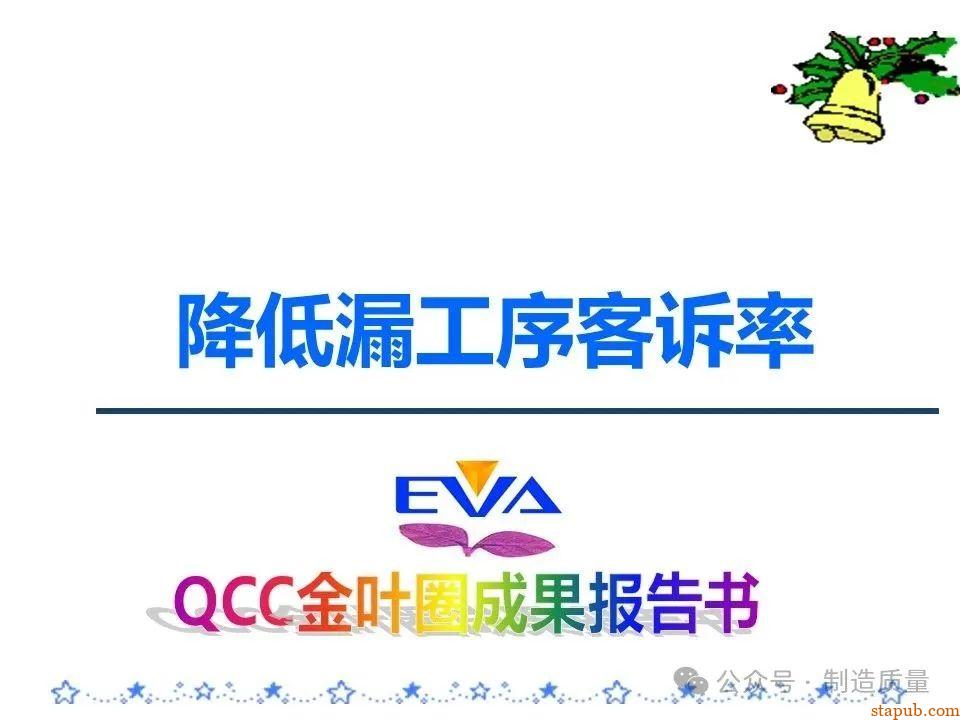
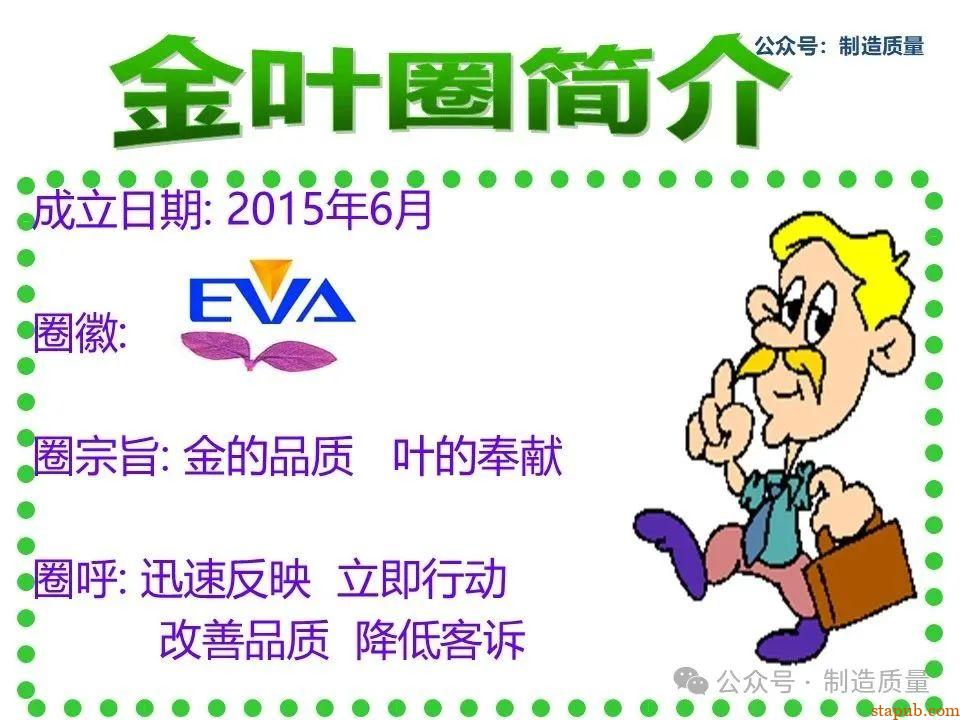
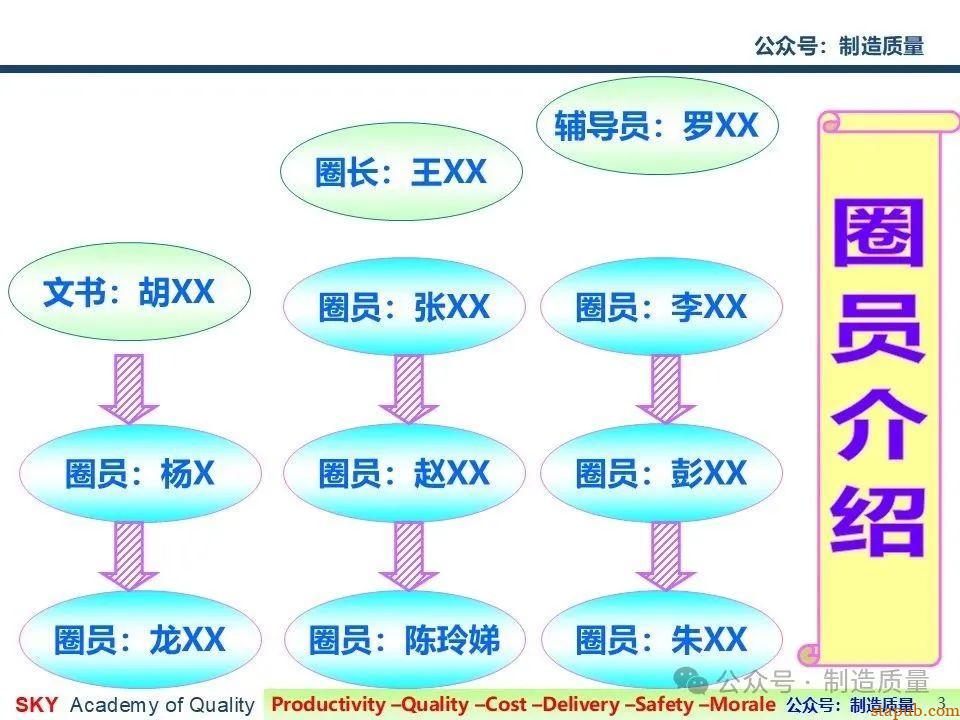
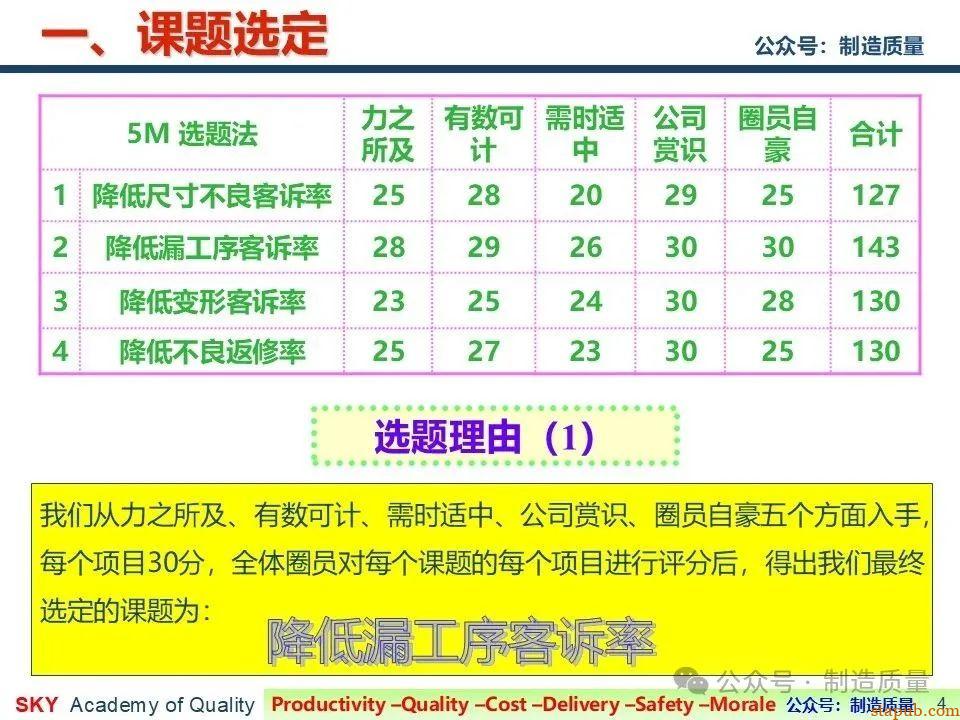
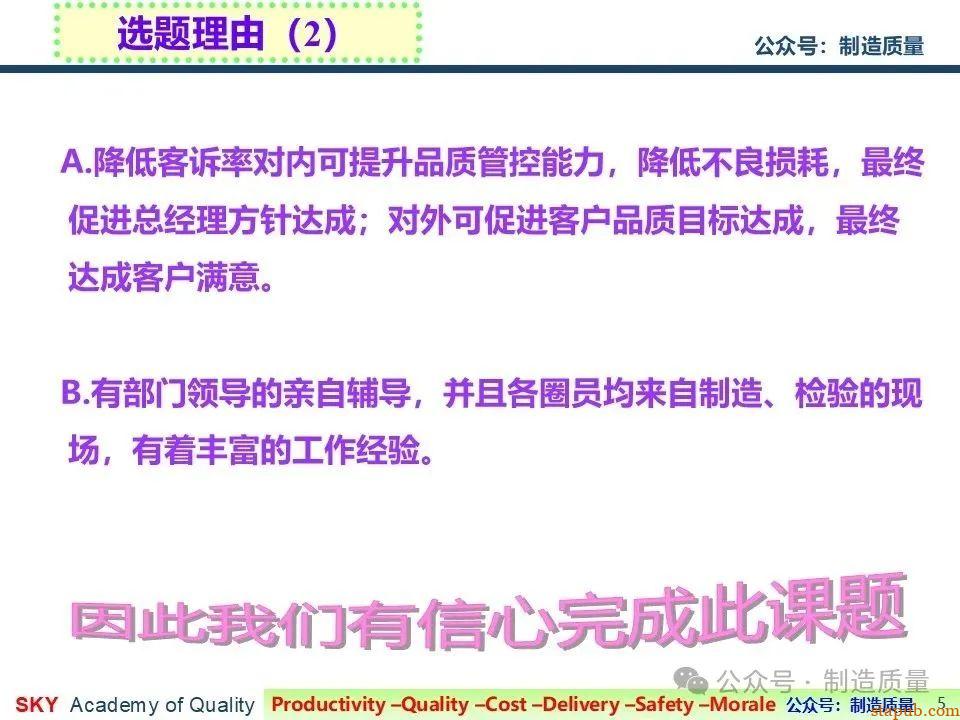
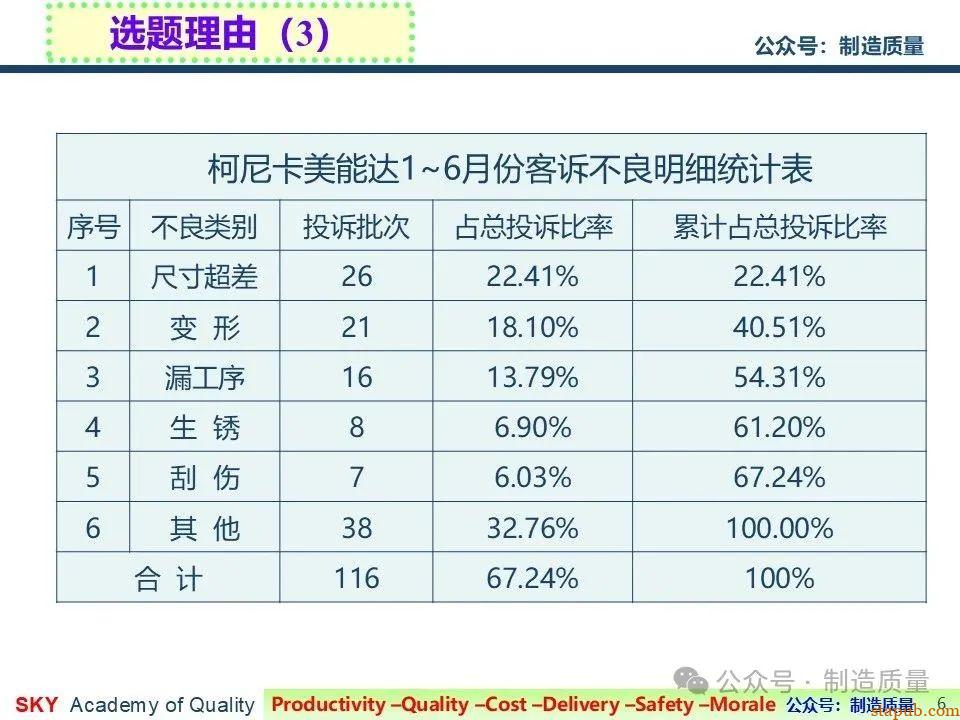
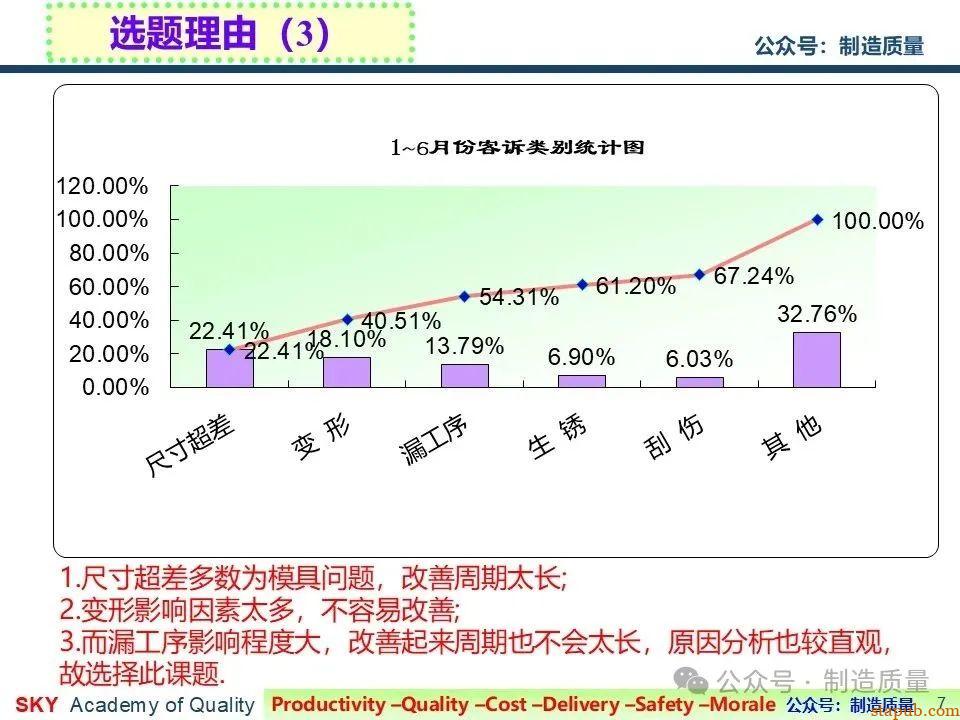
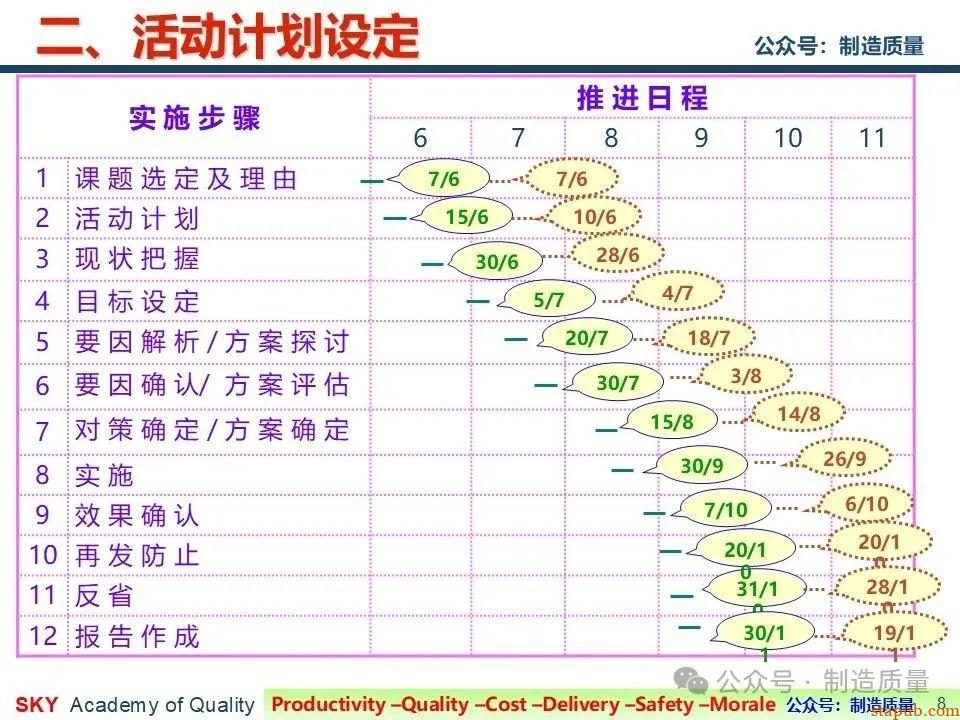
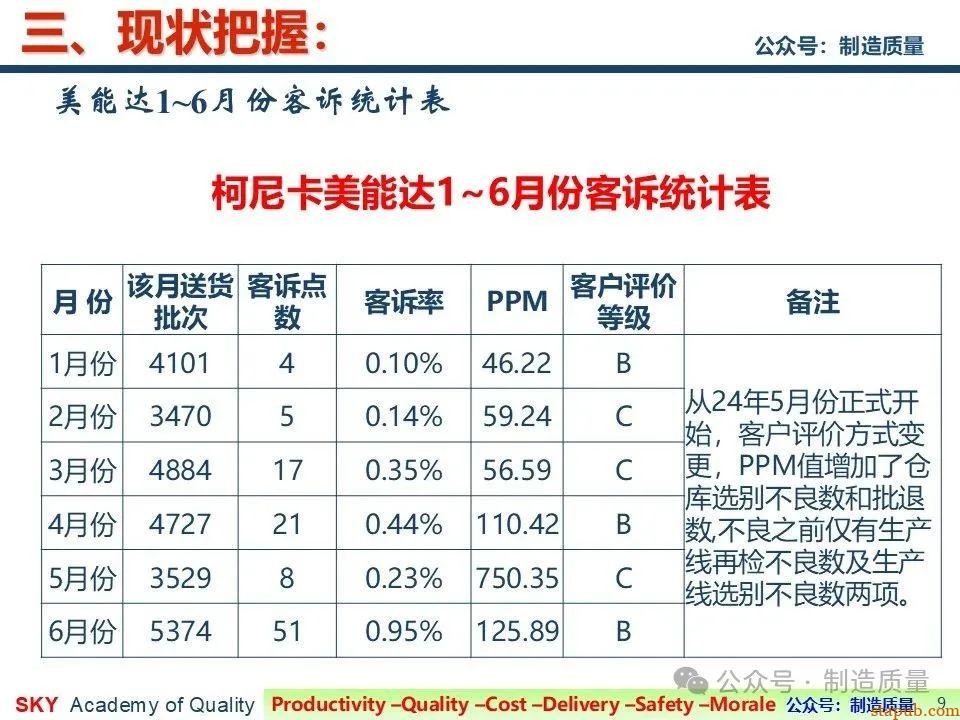
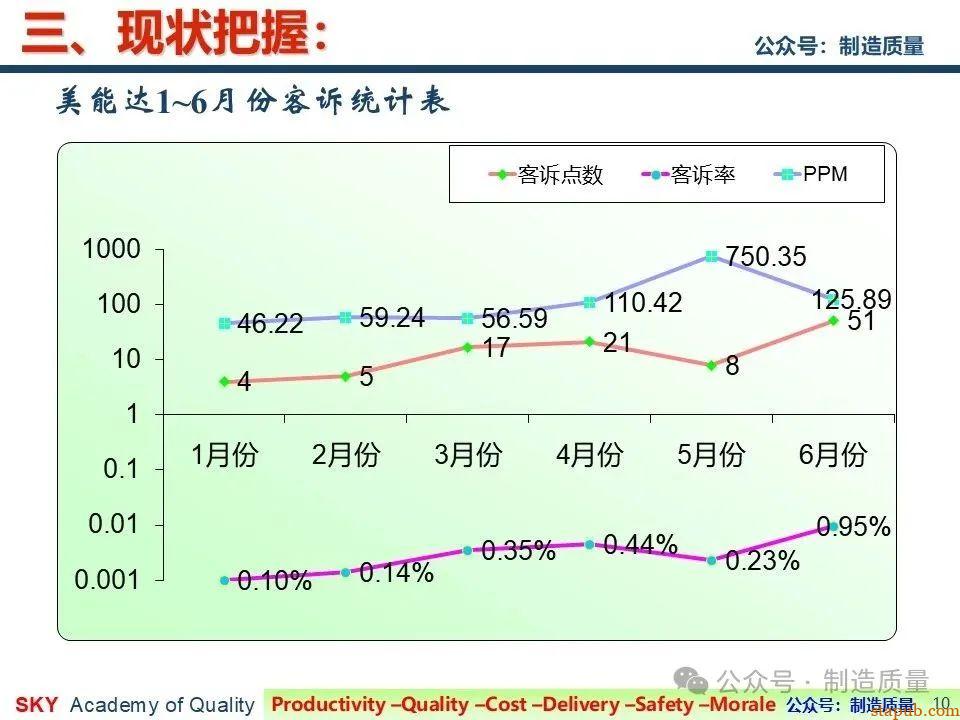
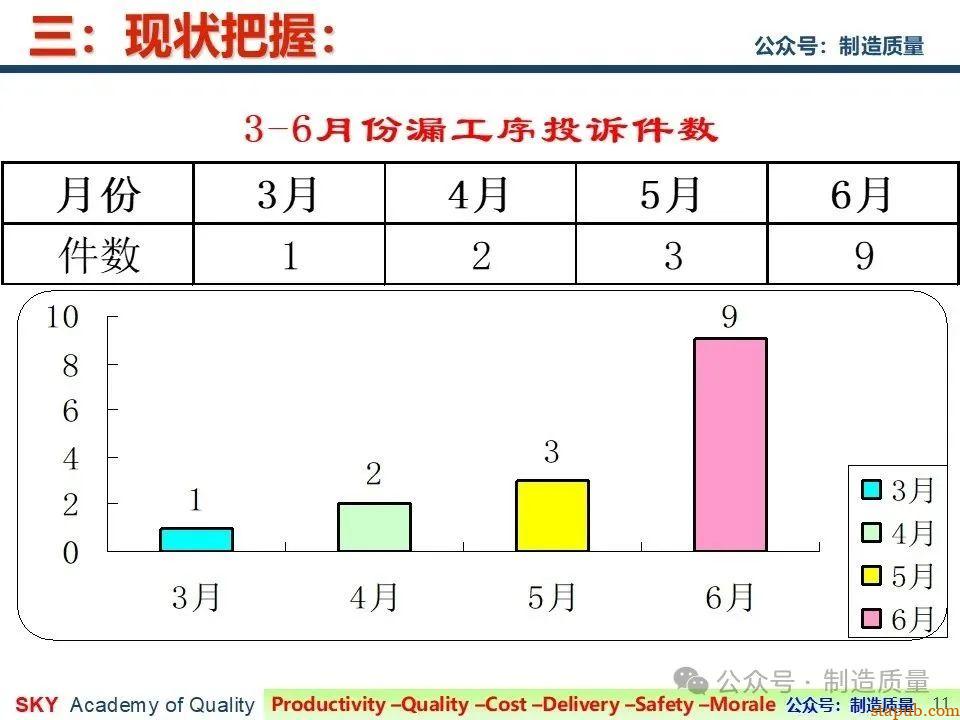
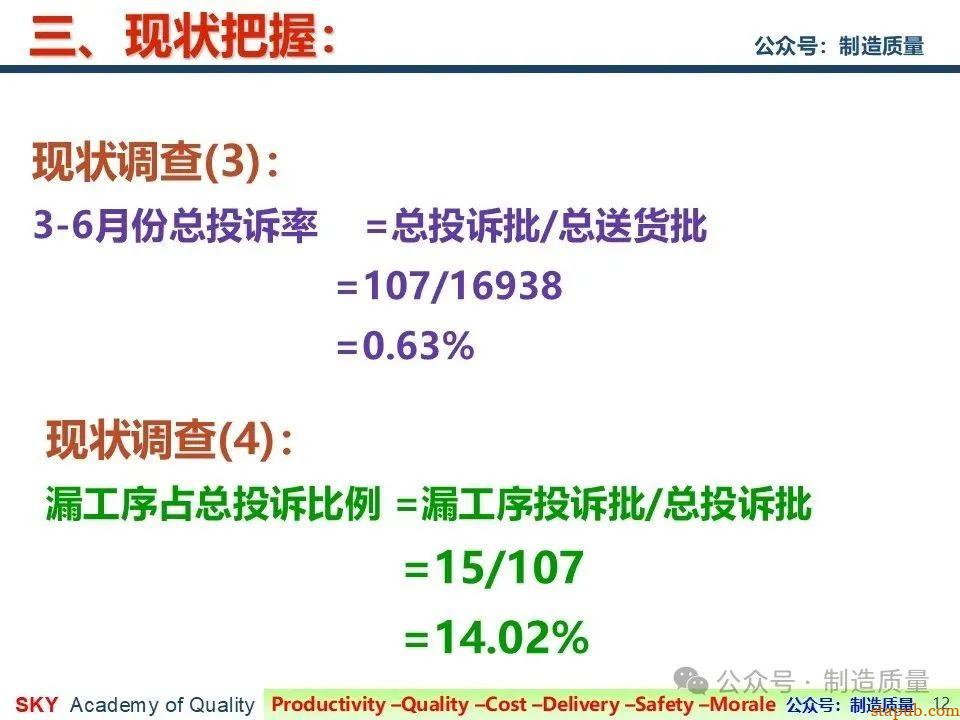
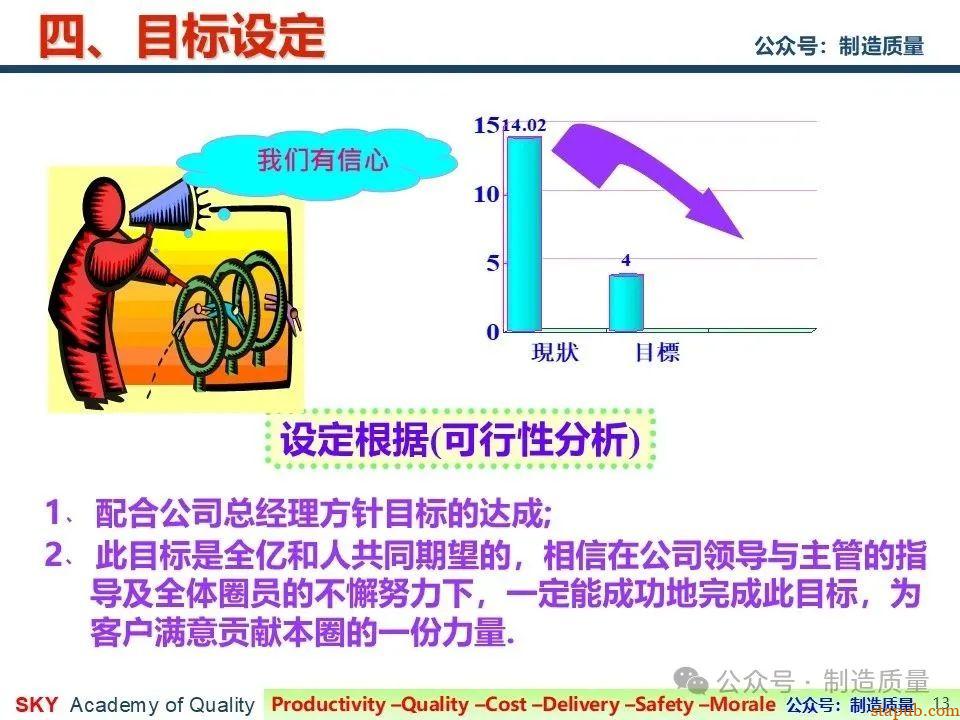
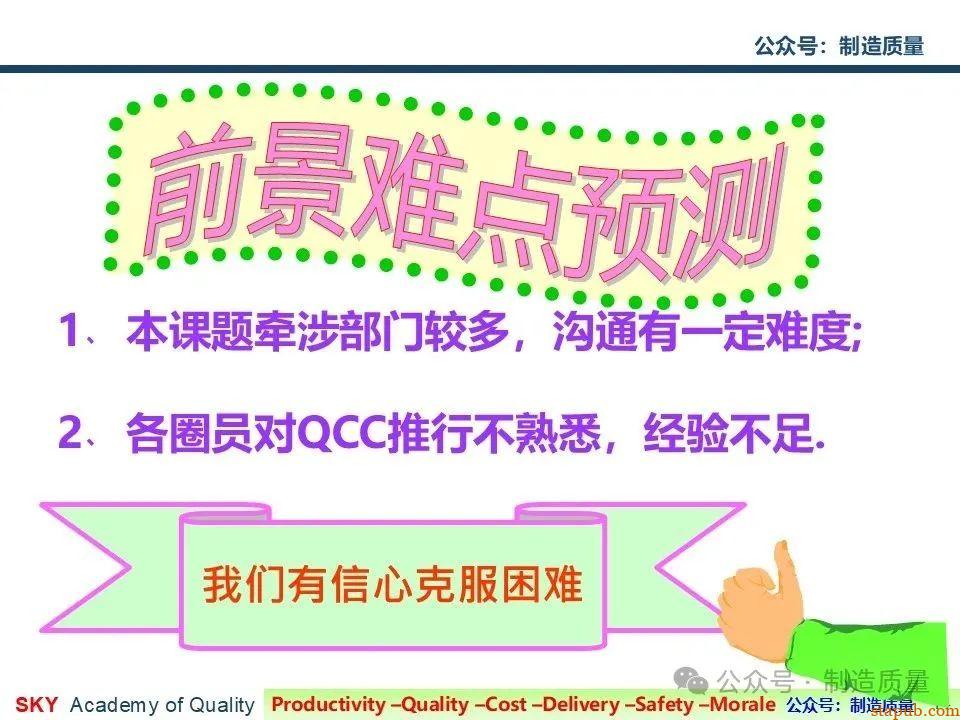
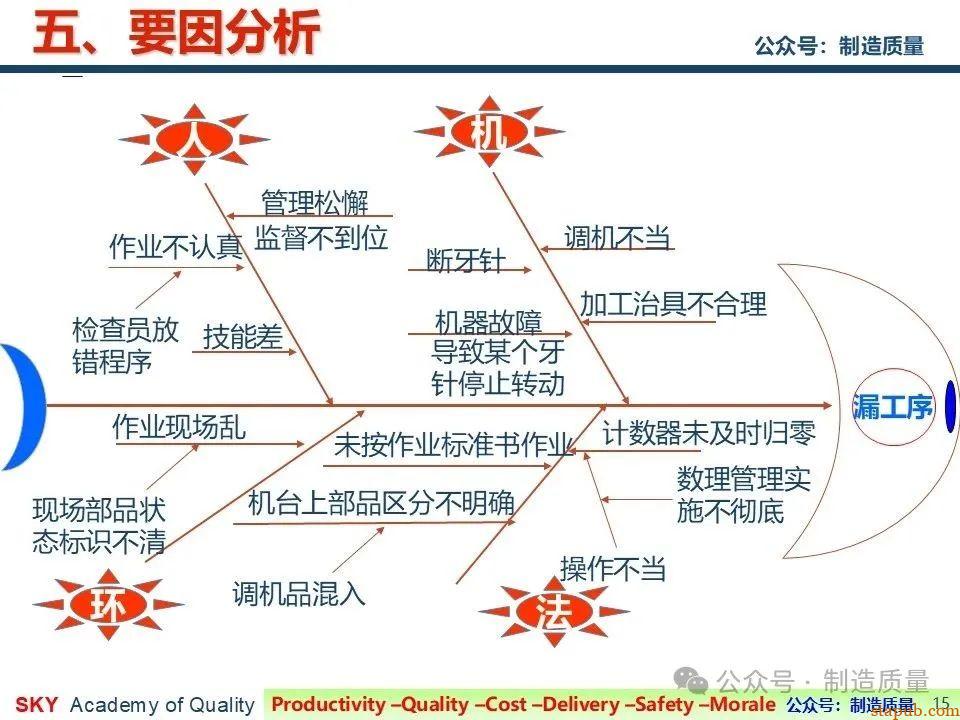
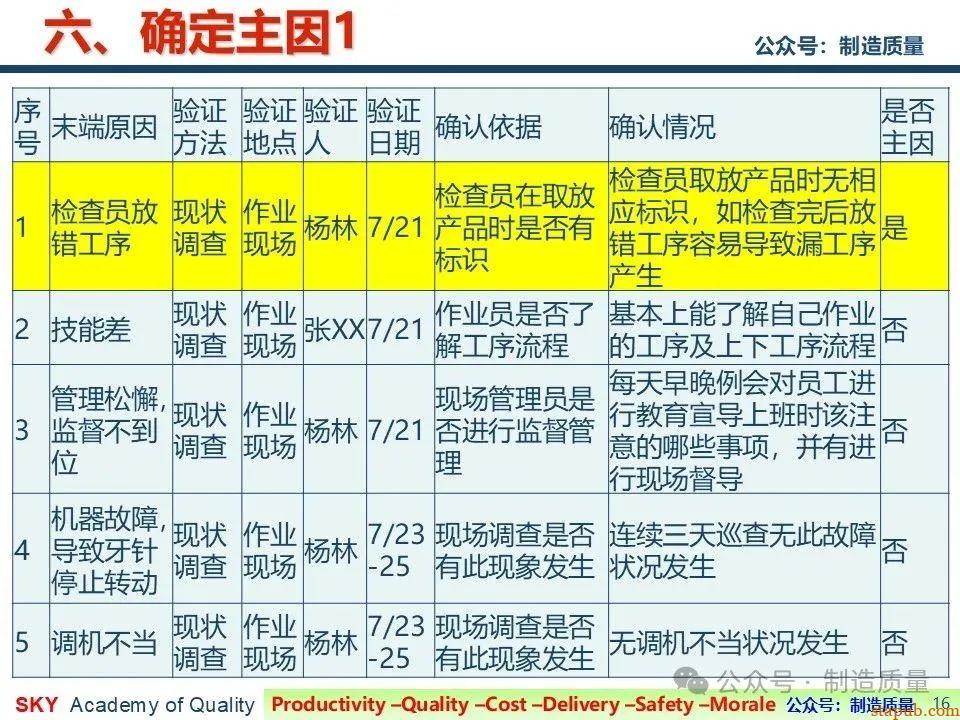
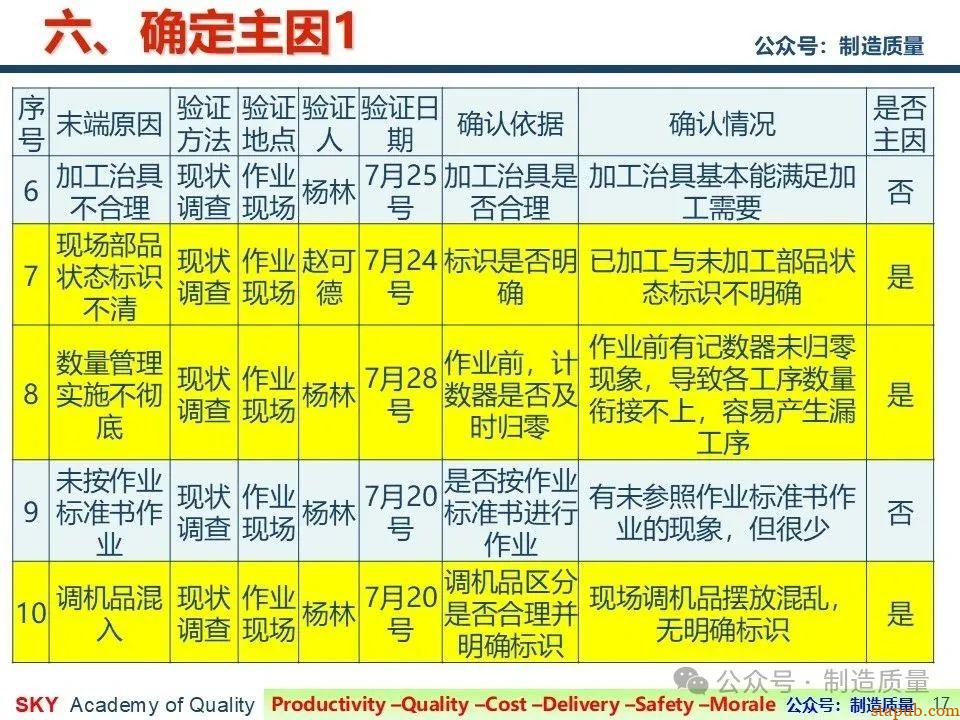
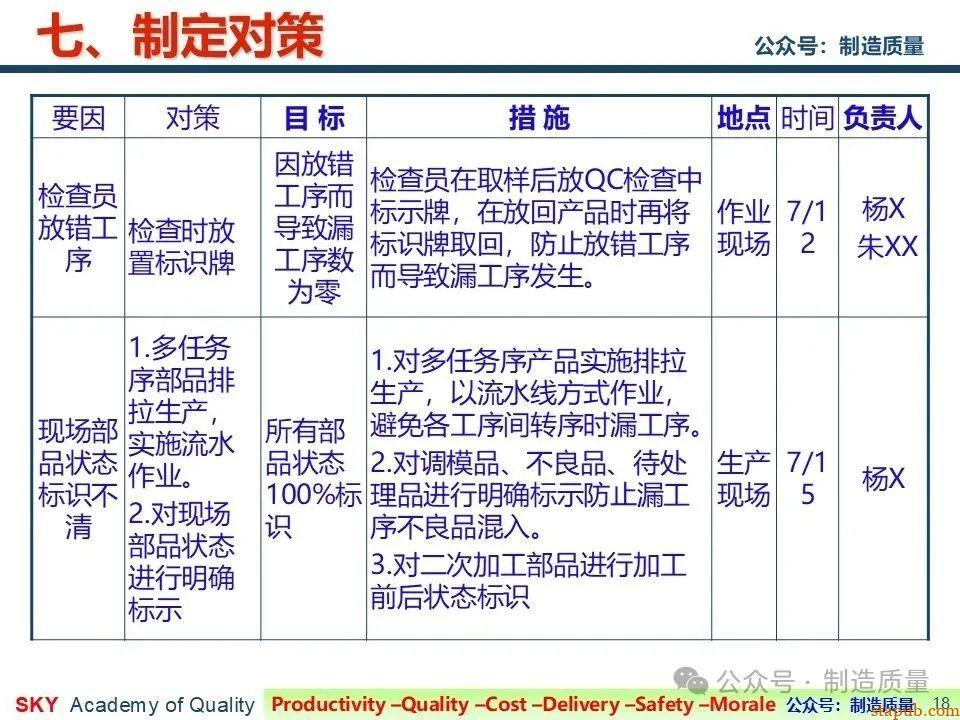
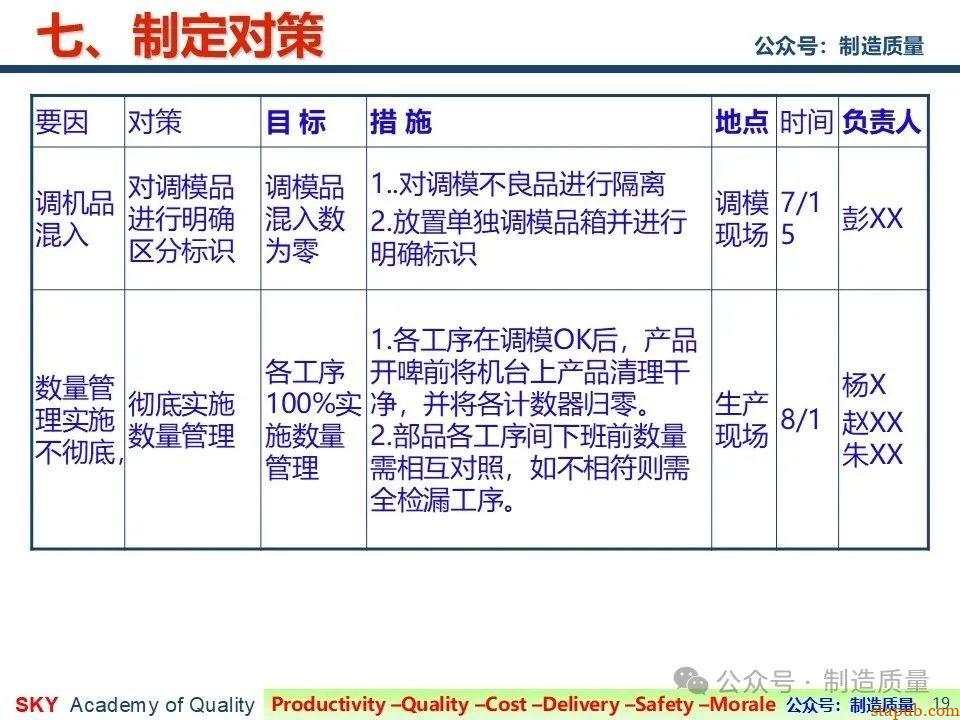
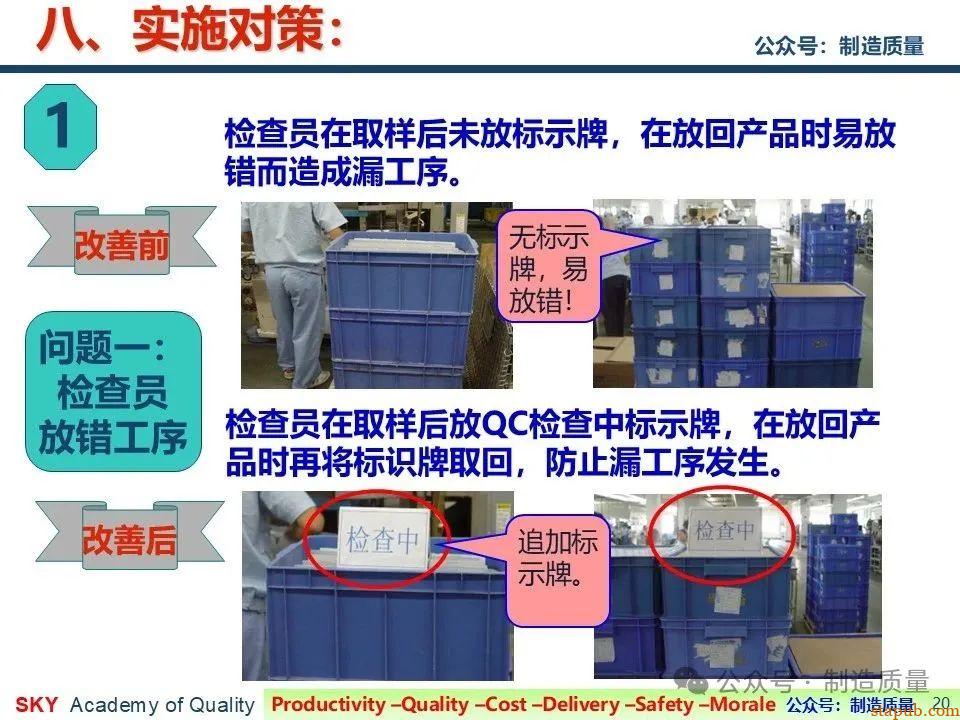
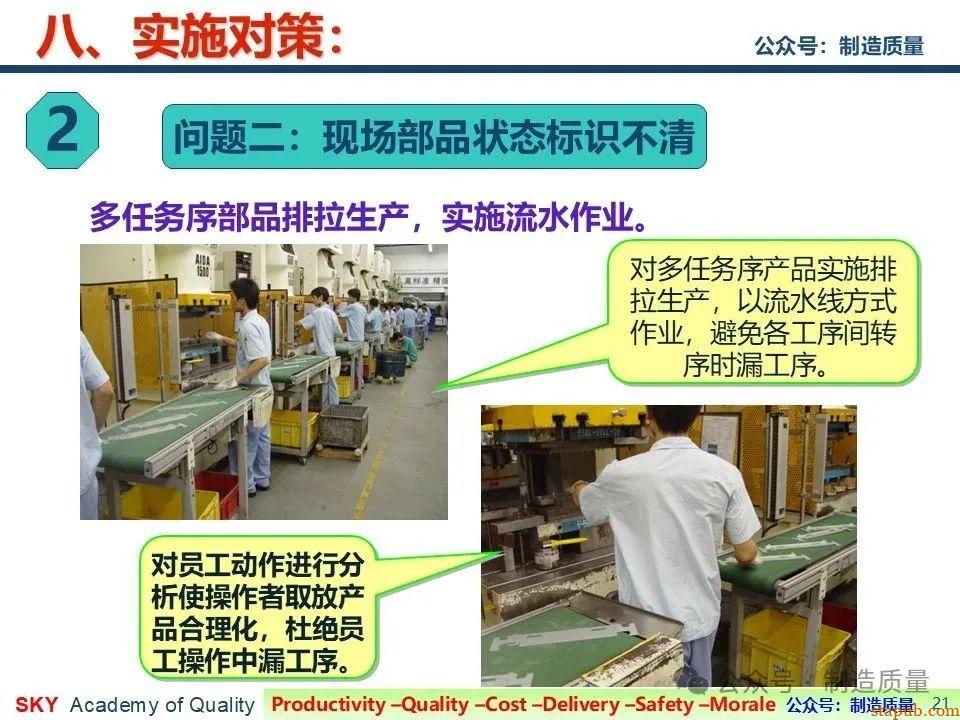
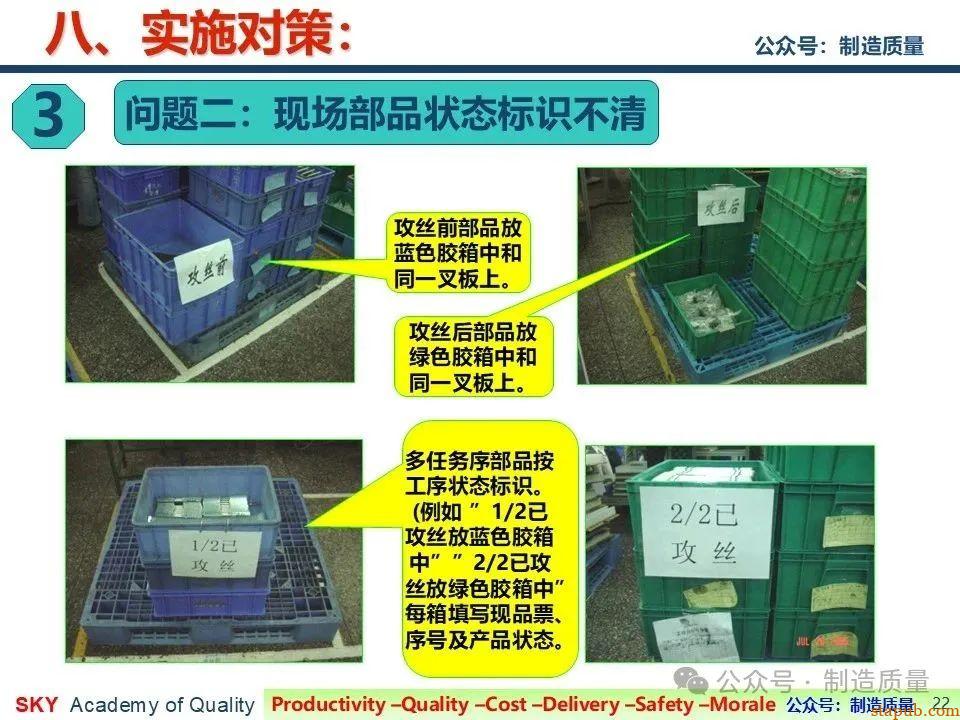
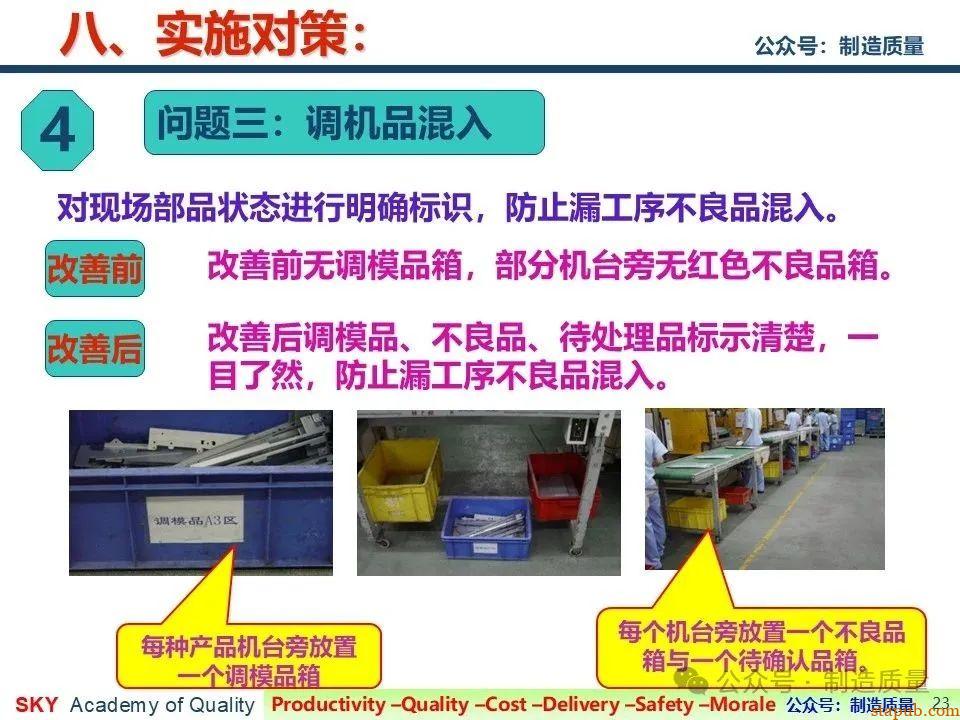
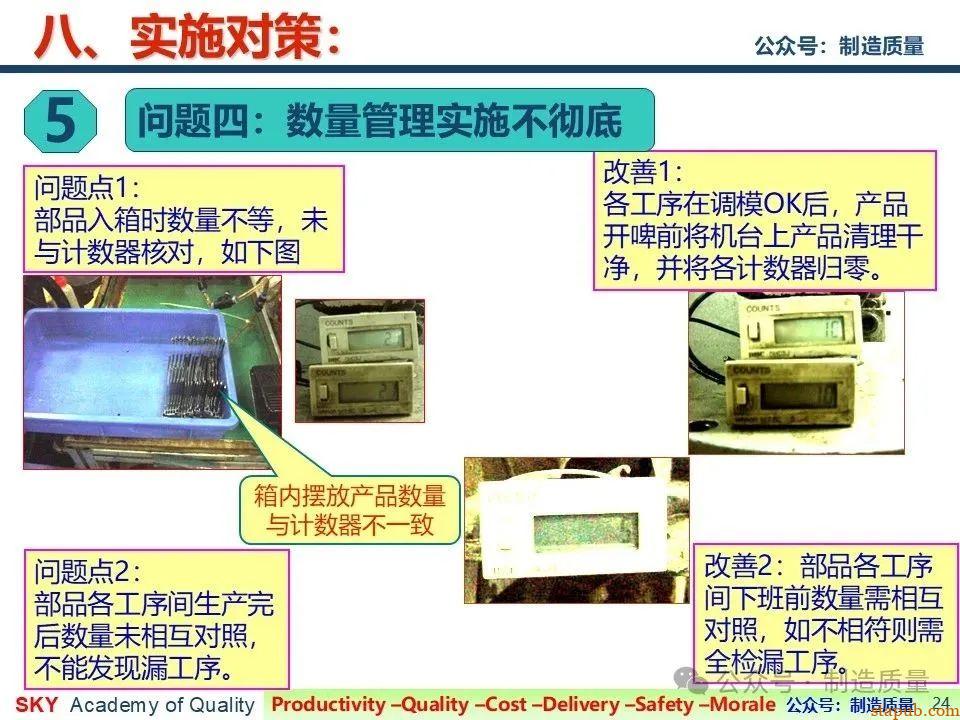

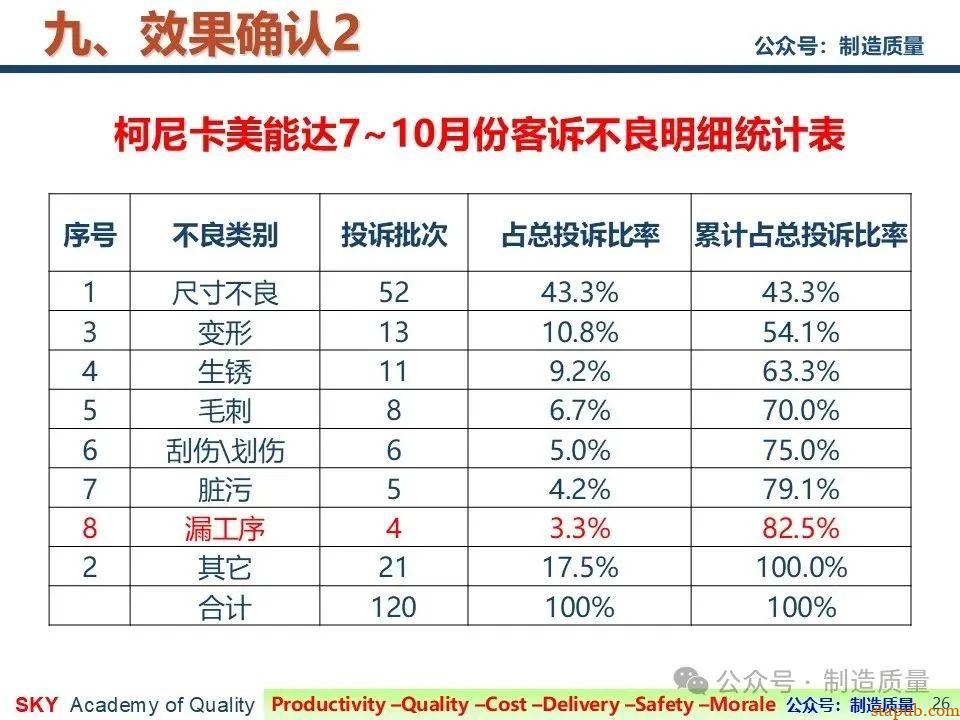
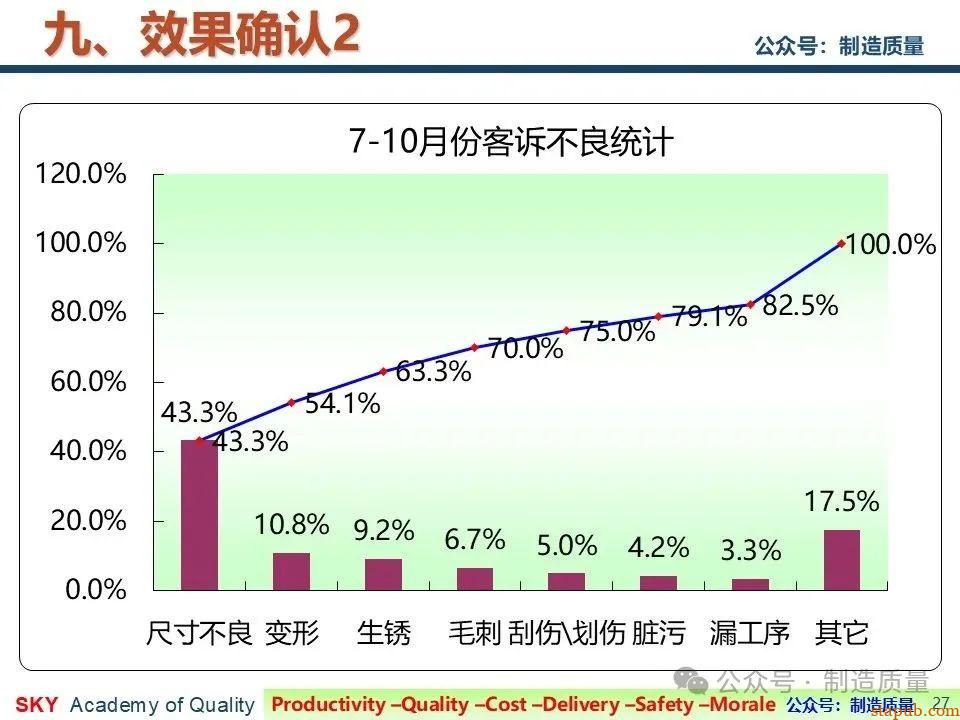
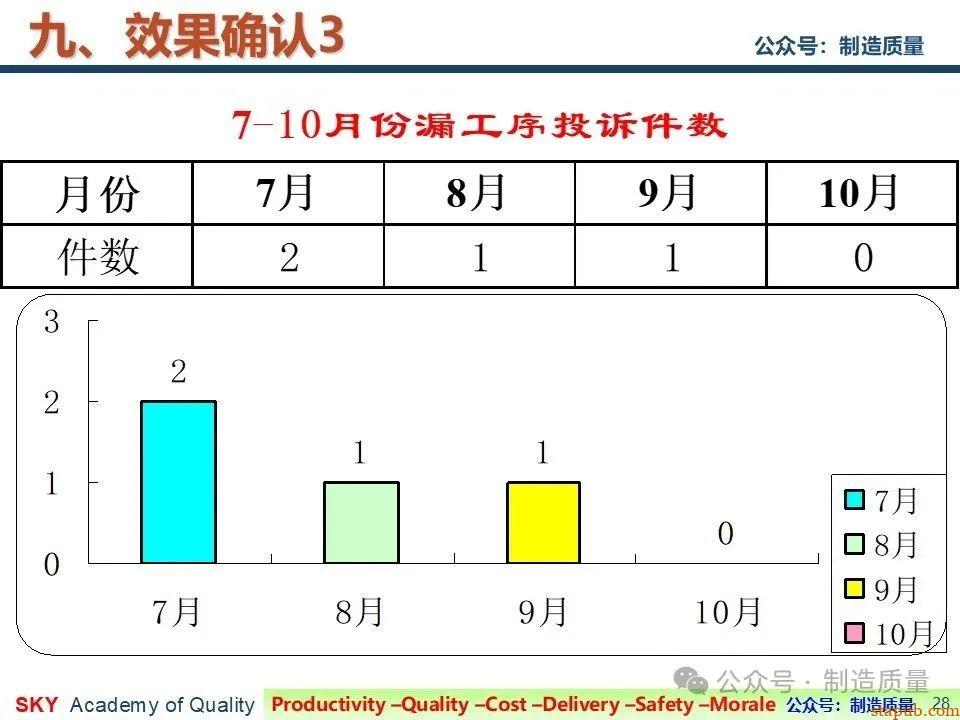
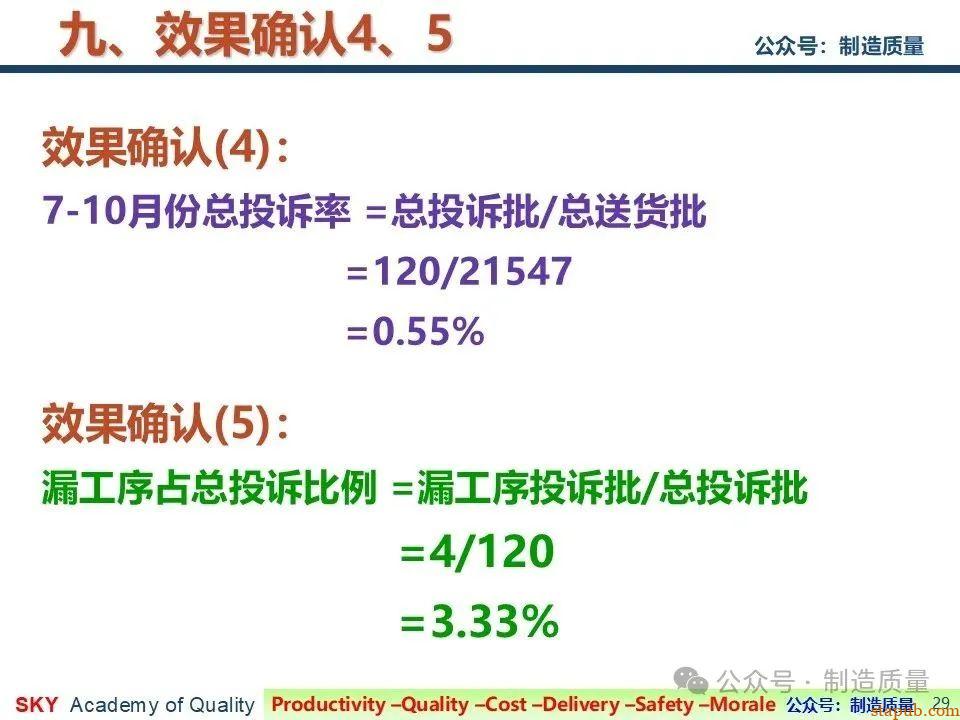
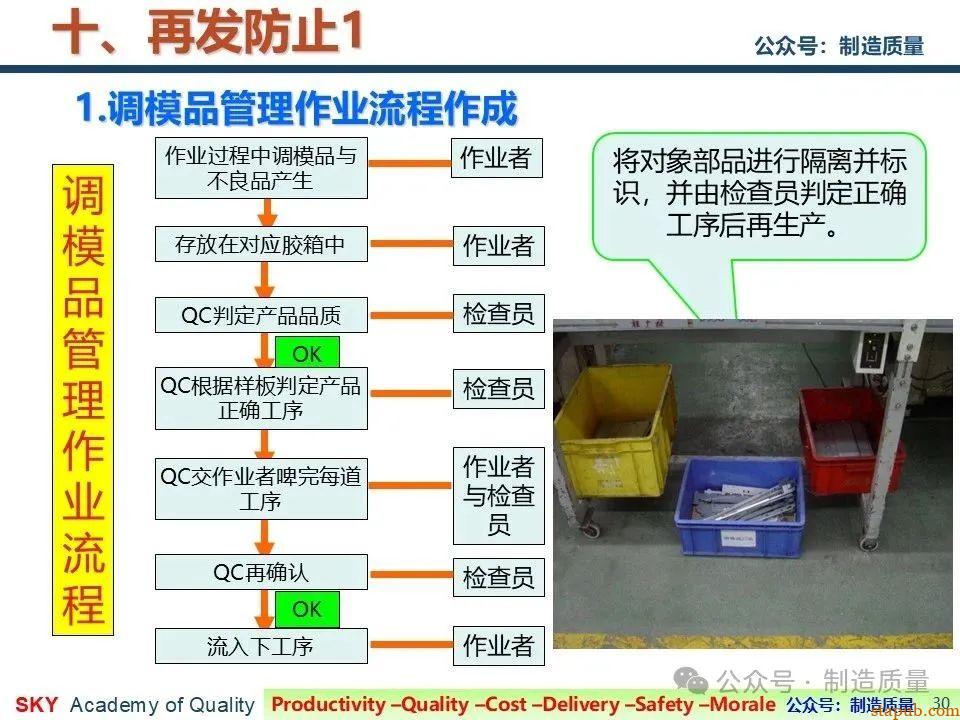
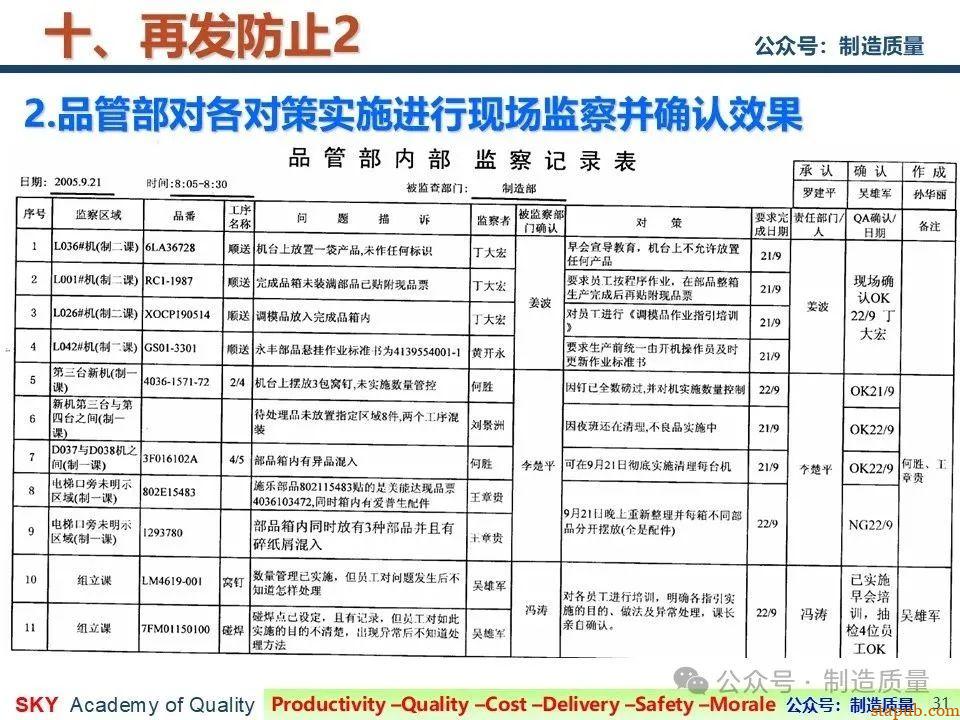
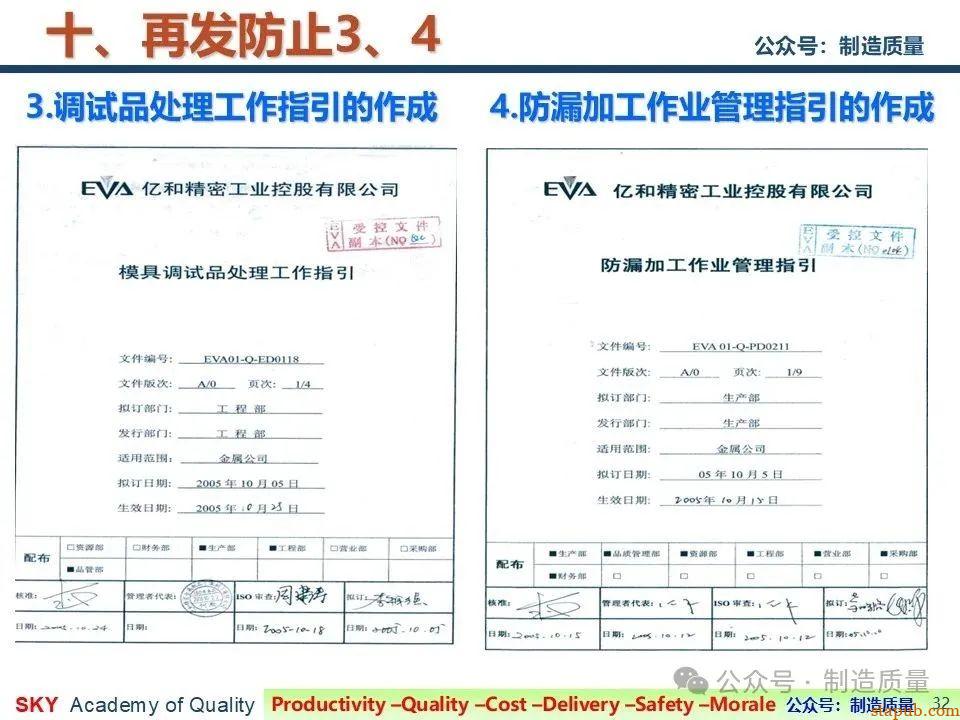
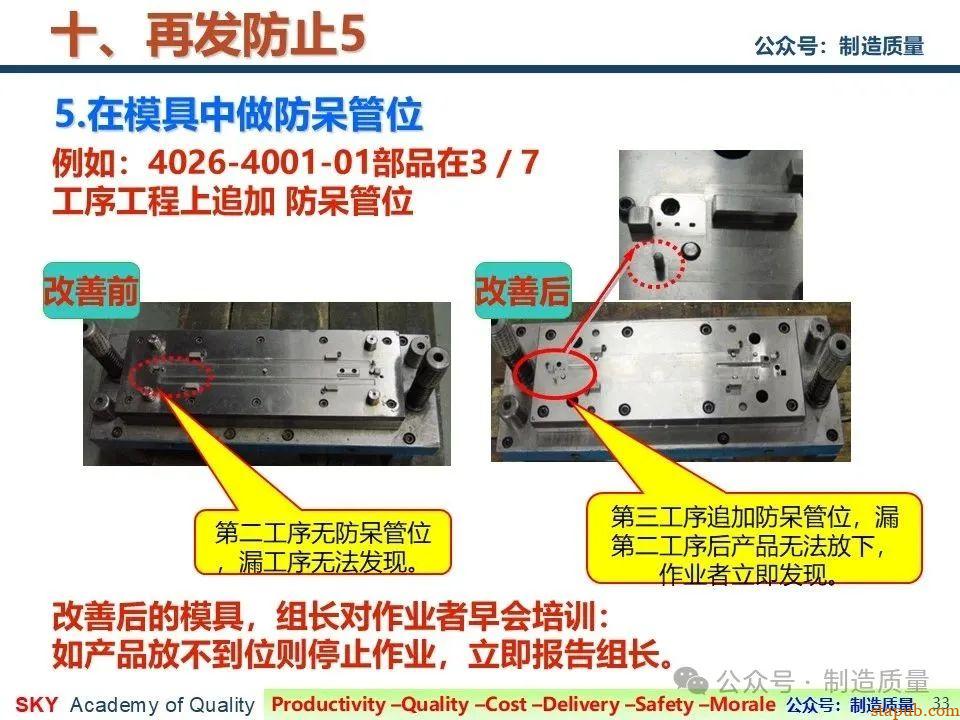
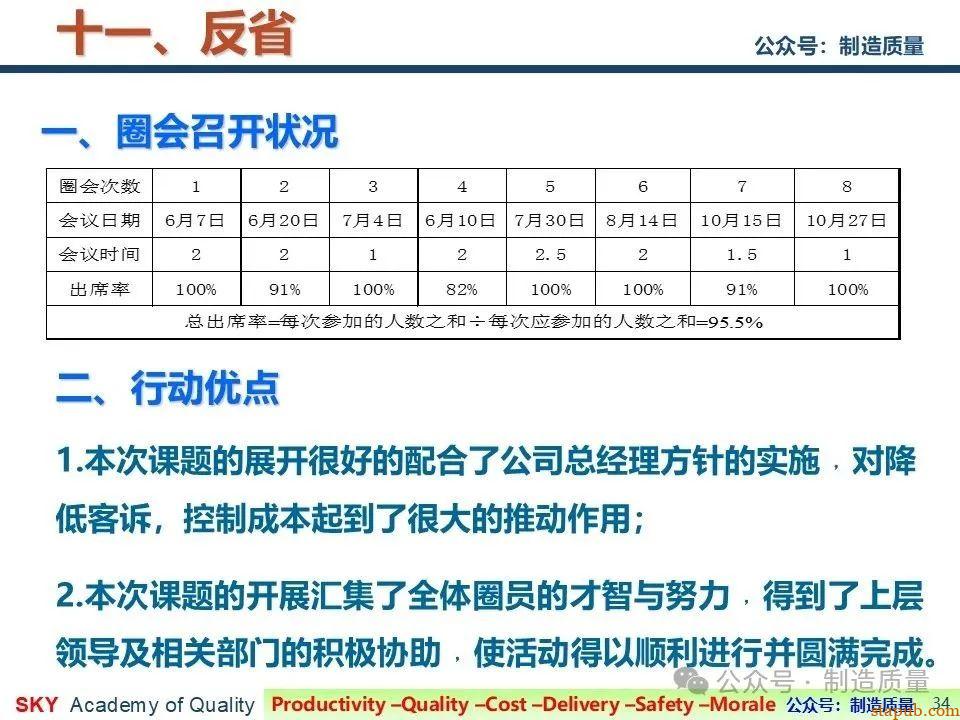
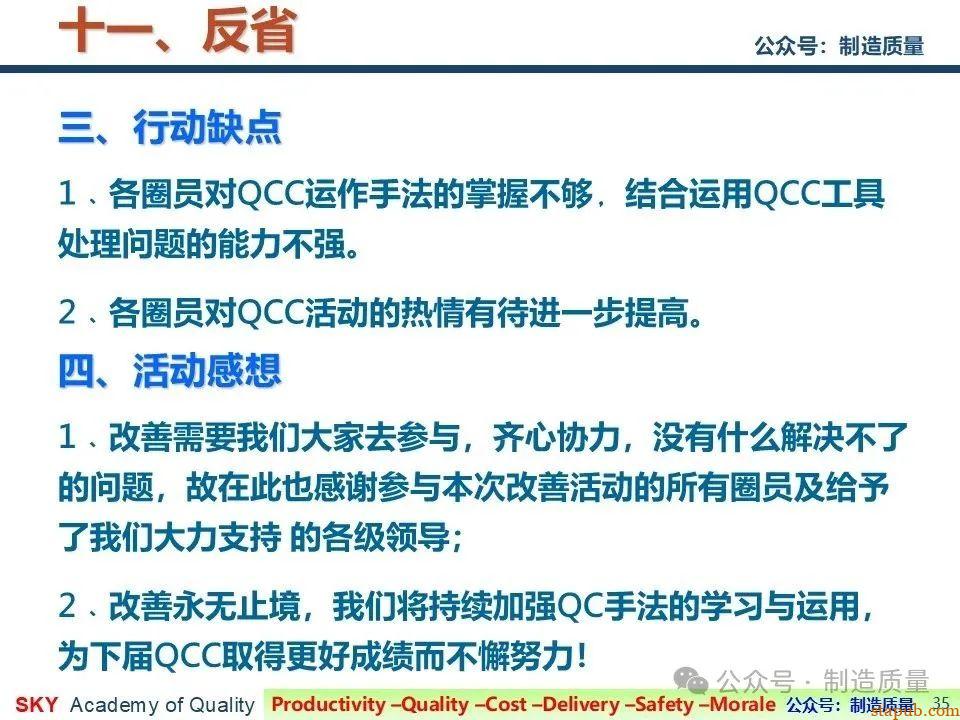