共计 1962 个字符,预计需要花费 5 分钟才能阅读完成。
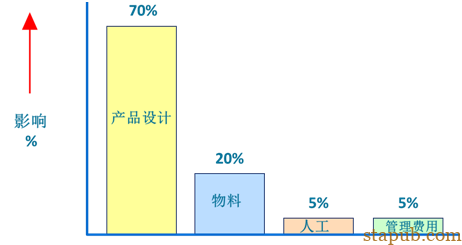
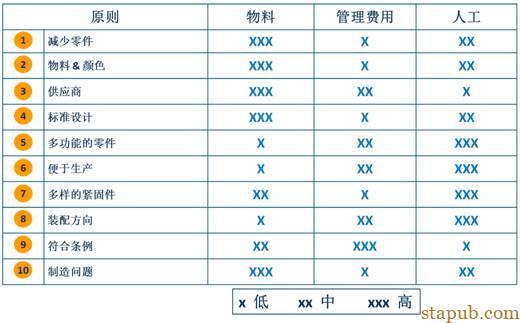
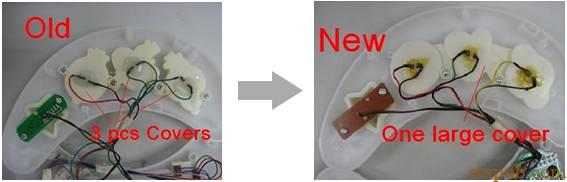
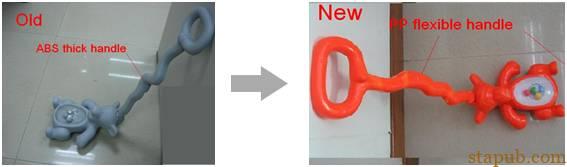
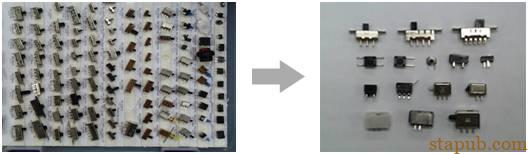
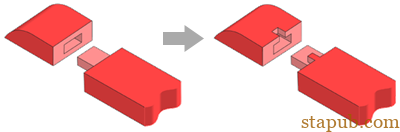
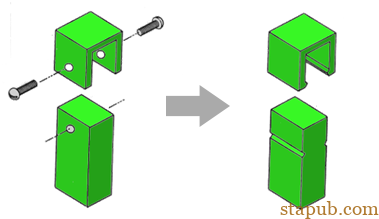
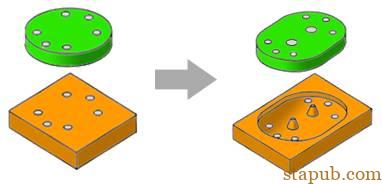
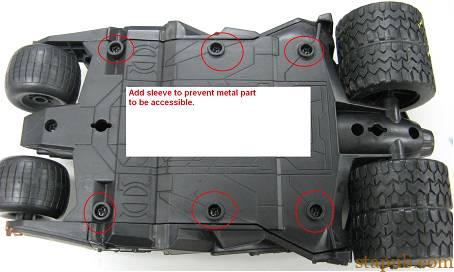
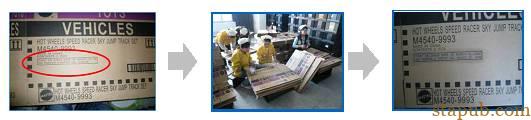
DFM 不是校对的步骤,其应该本身固有 DFM 不是只由“DFM工程师”做,是所有人都有责任 DFM 不是一个“工具”,而是一个 “思想” DFM 不只是在零件的阶段要考虑,在系统中有更多的地方要考虑 DFM 不是一个事后的想法,要把它当作一个得益之处 DFM 不是在以后的设计评论中才提到 DFM 不应熟练地应用于修改中,太迟了
来源:网络
正文完
共计 1962 个字符,预计需要花费 5 分钟才能阅读完成。
DFM 不是校对的步骤,其应该本身固有 DFM 不是只由“DFM工程师”做,是所有人都有责任 DFM 不是一个“工具”,而是一个 “思想” DFM 不只是在零件的阶段要考虑,在系统中有更多的地方要考虑 DFM 不是一个事后的想法,要把它当作一个得益之处 DFM 不是在以后的设计评论中才提到 DFM 不应熟练地应用于修改中,太迟了
来源:网络