共计 1165 个字符,预计需要花费 3 分钟才能阅读完成。
一、四轮定位核心参数体系
1.1 基本定位参数定义
|
|
|
---|---|---|
前束角 |
|
|
外倾角 |
|
|
主销后倾角 |
|
|
主销内倾角 |
|
|
推进角 |
|
|
1.2 参数功能关联矩阵
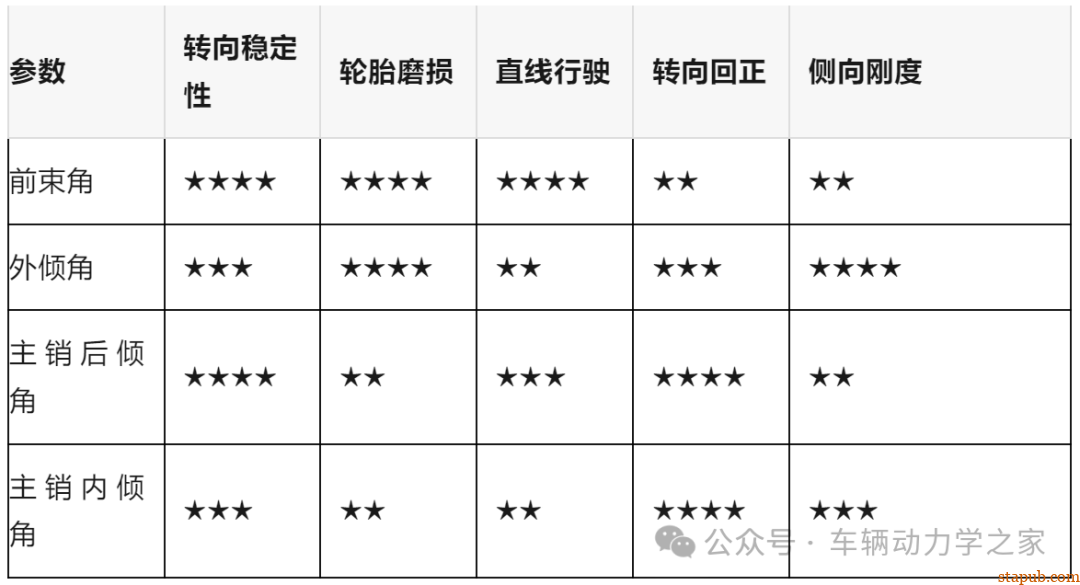
二、参数设计方法论
2.1 设计流程框架
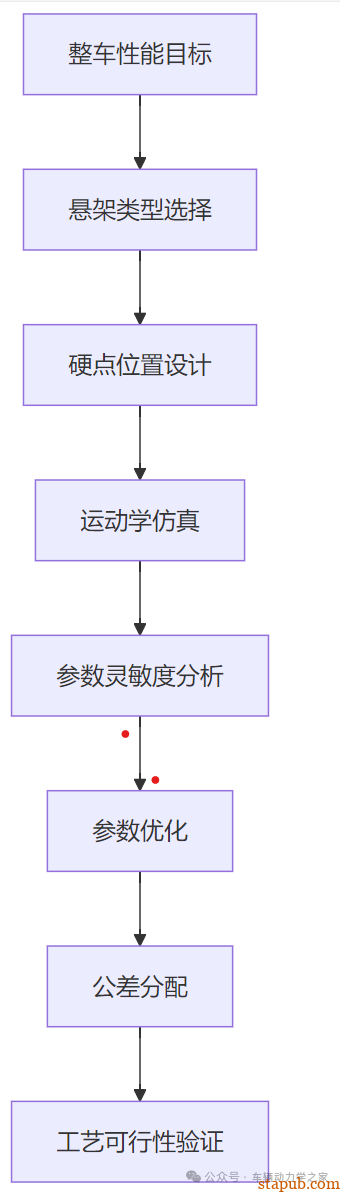
2.2 关键设计原则
- 前束角设计:
- 前驱车:轻微前束(0.1°~0.3°)补偿驱动力矩
- 后驱车:轻微后束(-0.1°~0°)减少转向过度
- 电动车辆:考虑再生制动扭矩影响
- 外倾角优化:
- 运动车型:负外倾(-1.0°~-0.5°)提升弯道抓地力
- 家用车型:接近0°或微正外倾优化轮胎磨损
- 重载车辆:动态外倾补偿设计
- 主销参数匹配:
- 后倾角与转向力矩的线性关系(每增加1°,转向力矩增加约5%)
- 内倾角与回正力矩的二次方关系
2.3 先进设计工具
- 多体动力学软件:ADAMS/Car, CarSim
- 参数化建模平台:CATIA DMU Kinematics
- AI优化算法:NSGA-II多目标优化
- 数字孪生系统:实时参数迭代验证
三、公差控制体系
3.1 制造公差要求
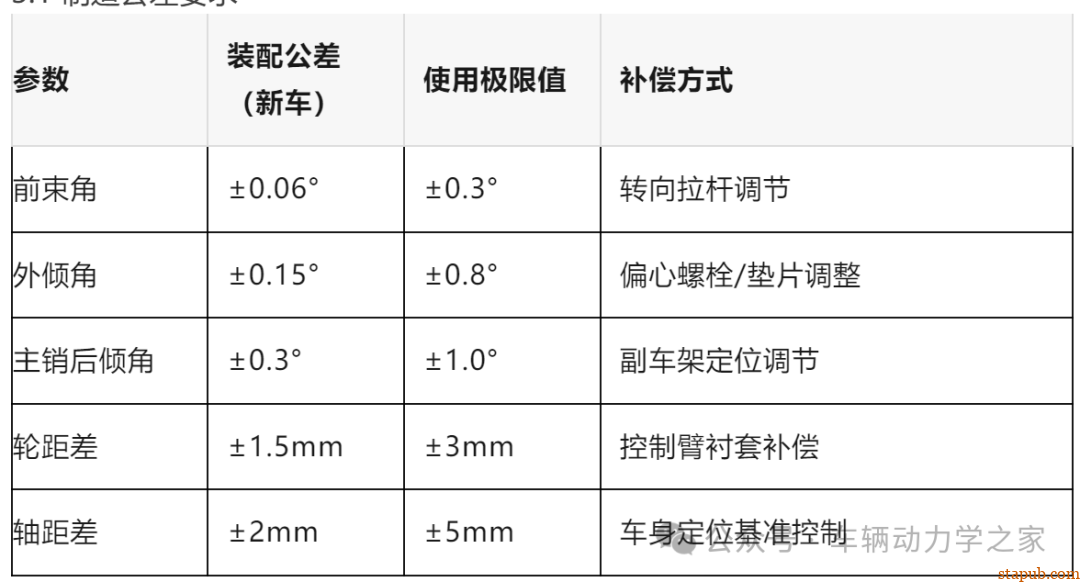
3.2 公差分配方法
- 敏感度分析:通过DOE确定各参数对性能的影响权重
- 成本-精度平衡:关键参数(如前束)采用更高精度控制(±0.03°)
- 累积误差控制:采用3DCS等软件进行尺寸链分析
- 动态补偿设计:对悬架柔性变形进行预补偿
3.3 关键控制点
- 基准体系建立:
- 车身定位孔精度:±0.1mm
- 副车架安装面平面度:0.15mm/m²
- 装配工艺控制:
- 拧紧顺序对硬点位置的影响
- 衬套预紧力控制(±5%)
四、典型问题解决方案
4.1 参数漂移问题
- 现象:行驶后参数超差
- 解决方案:
- 衬套刚度优化(静刚度提升20%~30%)
- 硬点加强设计(局部刚度增加50%)
- 采用液压衬套动态补偿
4.2 特殊工况应对
- 越野车辆:
- 加大公差范围(前束±0.4°)
- 采用可调式转向拉杆
- 高性能跑车:
- 缩小公差带(外倾±0.05°)
- 使用碳纤维定位支架
五、发展趋势
5.1 智能四轮定位技术
- 在线自适应调整:
- 基于路面识别的参数动态优化
- 48V主动悬架实时补偿
- 预测性维护系统:
- 通过轮速传感器数据预测参数偏差
- 提前50%里程预警
5.2 新型制造技术
- 激光熔覆定位基准:将定位精度提升至±0.01mm
- 磁流变衬套:刚度可调范围扩大300%
- 量子测量技术:检测精度达到纳米级
结语
四轮定位参数设计是机械精度与系统动力学的完美结合,现代设计已从静态几何匹配发展到动态智能调控阶段。公差控制需贯穿产品全生命周期,通过”设计-制造-检测-维护”的闭环控制,实现纳米级精度的工程控制。未来随着线控底盘技术的普及,四轮定位将突破物理约束,进入”软件定义定位”的新纪元,为智能出行提供更精准的操控基础。
正文完