共计 1956 个字符,预计需要花费 5 分钟才能阅读完成。
在注塑模具中,流道系统是连接注塑机喷嘴与型腔的关键通道,其作用是将熔融塑料平稳、均匀地输送至型腔并充满。
流道系统主要由主流道、分流道、浇口及辅助的冷料穴组成。不同类型的流道适用于不同场景,开模时的选择需结合制品特性、材料、生产需求等综合判断。
01
注塑模具流道的类型及适用场景
首先,按流道在模具中的结构与功能划分,可分为主流道、分流道和浇口。
主流道是熔融塑料从注塑机喷嘴进入模具的第一道通道,直接与喷嘴接触,形状为圆锥形(便于凝料脱模)。
结构特点:通常为圆锥形(锥度1°~3°),便于凝料脱模;入口端与喷嘴匹配(直径略大于喷嘴直径0.5~1mm),末端连接分流道或浇口。
作用:承接注塑机喷出的熔体,初步引导至模具内部,是流道系统的“主干”。
适用场景:所有模具均需主流道,单型腔模具中主流道可直接连接浇口,多型腔模具中主流道需通过分流道分配熔体。
分流道是主流道与浇口之间的通道,用于将熔体分配到多个型腔(多型腔模具)或单型腔的不同位置。常见截面形状有以下几种:
圆形,截面积最大,熔体流动阻力最小(效率最高),但加工难度大(需两板模合模后加工,成本高),适用于高流动性材料或长距离输送;
梯形,加工简单(可单板加工),效率接近圆形,是最常用的类型(梯形高与宽比约3:4);
U 形/半圆形,流动性略差于圆形和梯形,但加工更简单,适用于低要求场景;
矩形,流动阻力较大,仅在特殊结构(如薄型制品)中偶尔使用。
浇口是连接分流道与型腔的狭窄部分,是流道系统的“咽喉”,直接控制熔体进入型腔的速度、时间和压力,同时便于开模时切断凝料。按结构可分为以下常见类型:
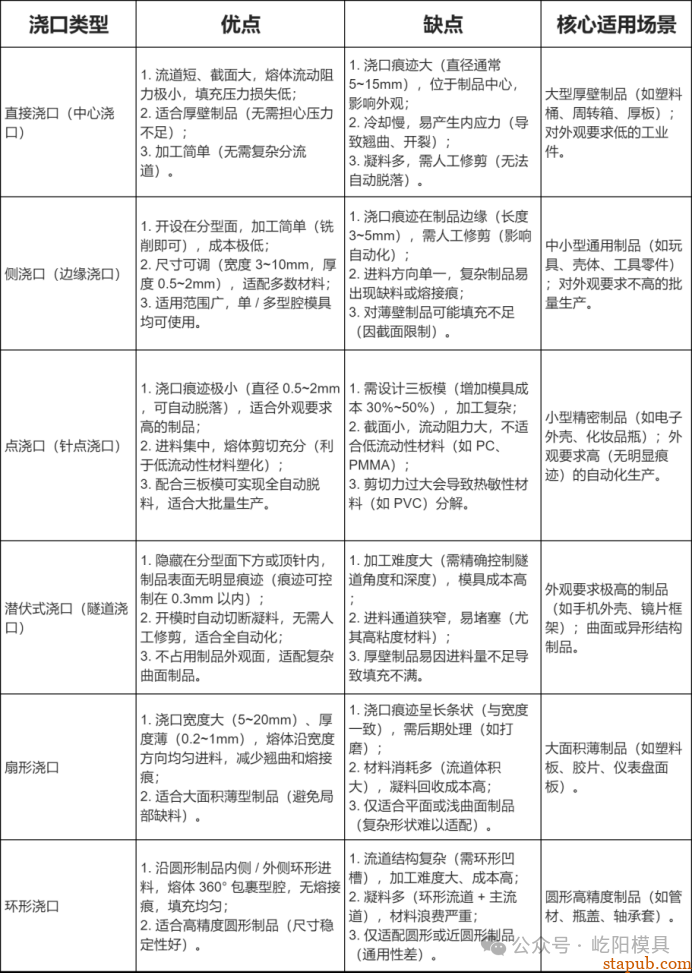
其次,按流道是否加热划分 ,可分为冷流道和热流道
冷流道是传统流道,无加热装置,熔体在流道中随模具冷却而凝固(形成 “流道凝料”),开模后与制品一同取出。
结构特点:由主流道、分流道组成,材质与模具型腔一致,多为P20、718H等模具钢,依赖模具本身的冷却系统降温。
优点:
模具结构简单,加工成本低,比热流道低30%~60%;
适配所有塑料,尤其热敏性材料,如PVC,避免过热分解;
维护方便,无需额外加热元件。
缺点:
流道凝料占比高,约10%~30%的材料浪费,需回收处理;
凝料脱模后需人工分离,影响自动化效率;
熔体在流道中冷却导致温度下降,可能增加填充压力(尤其长流道场景)。
适用场景:小批量生产、多品种切换频繁、热敏性材料、低成本需求的模具,如日用品、低精度工业件。
热流道通过加热装置(加热圈、加热棒)使流道内的熔体始终保持熔融状态,开模后无流道凝料(仅制品脱出)。
结构组成:热流道板(加热分流道,保持熔体温度)、热喷嘴(连接热流道板与浇口,直接向型腔进料)、温控系统(精确控制各区域温度,误差±1℃以内)。
分类(按喷嘴结构):开放式热流道(喷嘴直接与型腔接触,浇口无阀针,结构简单,成本较低,但易产生“拉丝”或“流涎”,低粘度材料慎用)、针阀式热流道(喷嘴内有阀针,通过油缸/气缸控制浇口开关,可避免流涎,适合低粘度材料,如 PE、PP和高精度制品)。
优点:
无流道凝料,材料利用率达95%以上,节省成本; ◦
熔体温度稳定,填充压力损失小,适合薄壁、长流程制品;
可实现全自动生产(无凝料分离步骤),提升效率;
减少熔接痕,熔体无冷却凝固,流动性更稳定。
缺点:
模具成本高(比冷流道高 50%~200%),初期投入大;
需匹配温控系统,维护复杂(加热元件易损坏);
不适用于热敏性材料(长期加热易分解)或高填充材料(如玻纤增强塑料,易磨损喷嘴)。
适用场景:大批量生产(如饮料瓶胚、手机外壳)、高外观要求制品(无凝料痕迹)、薄壁精密件(如电子连接器)。
其他特殊流道类型
潜伏式流道(与潜伏式浇口配合):流道隐藏在模具分型面下方或顶针内部,与潜伏式浇口衔接,开模时流道凝料随顶出动作自动切断,兼顾外观(无表面痕迹)和自动化。
适用:外观要求高的复杂制品(如家电面板、汽车内饰件)。
扇形流道(与扇形浇口配合):流道末端呈扇形扩展,宽度逐渐增大、厚度减小,使熔体沿宽度方向均匀分布,减少大面积薄制品的翘曲和熔接痕。
适用:大面积薄型制品(如塑料薄膜、仪表盘面板)。
02
选择逻辑
1、成本优先。选冷流道(尤其小批量或多品种生产)。
2、效率与材料节省。选热流道(大批量、高附加值制品)。
3、多型腔一致性。优先平衡式分流道。
4、外观与自动化。选潜伏式流道(配合潜伏式浇口)或热流道(无凝料)。
实际设计需结合制品结构(尺寸、壁厚)、材料特性(流动性、热敏性)及生产批量综合判断,必要时通过模流分析模拟流道压力损失和填充均匀性。