共计 1870 个字符,预计需要花费 5 分钟才能阅读完成。
在质量管理体系中,SPC(统计过程控制)几乎是家喻户晓的工具。然而,真正能够将其用好、用出实际价值的从业者却屈指可数。许多人使用SPC,仅止于绘图展示,一旦数据点越出控制界限,便草率判定为“异常”,紧接着或是简单调整参数,或干脆忽略,通过重新采样让图表“好看”为止。这种做法将SPC沦为“面子工程”——图是画了,流程问题却毫无触动。
当SPC图表显示异常后,应查什么?从哪里查?如何追溯到流程的根本性问题?
这才是具备真正“SPC应用能力”的人员应当掌握的内容。

SPC的核心价值并非仅用于识别异常,而在于借助统计信号提前发现潜在流程偏差,实现预防性干预与持续改善。
现实中,许多一线或工程技术人员对SPC的认知停留在浅层操作上:
-
会生成控制图;
-
了解基本的判异规则。
一旦图表出现异常,便陷入无从应对的困境:
-
异常点具体对应哪个流程节点?
-
判异信号与现场作业、设备、原材料之间有何关联?
-
责任划分该如何界定?溯源范围应覆盖哪些时间段?
这些问题的应对能力,取决于两个基本功:
-
起点:数据采集是否准确、具有代表性?
-
终点:是否具备将数据异常反推至流程问题的能力?
SPC的价值链条,恰恰建立在这两端的扎实基础上。

SPC的八大判异规则,底层逻辑是一致的:
“在随机稳定过程中几乎不可能出现的事件”,一旦发生,意味着流程高度可疑,必须引起注意。
以第一条规则为例:“单点超出±3σ”,其在稳定过程中的理论概率仅为0.27%。因此,一旦出现该异常信号,说明该样本点极不可能是随机波动,应高度警惕。
⚠️ 值得强调的是:异常点 ≠ 问题点
异常信号仅表示流程**“可能”**存在问题。后续仍需结合现场情况,按照“人、机、料、法、环、测”六大因素系统排查。

以下为各规则背后的可能原因与建议的溯源路径:
检验1|单点超出 ±3σ
-
均值图+散布图皆异常:说明极端偏差,可能为严重测量误差或突发性流程问题
排查方向:测量仪校准异常?样本操作错误?设备临时故障?是否为更换刀具或参数突调? -
仅均值图异常:表示系统性轻微偏移
排查方向:原料更换?设备状态轻微修复?工艺参数小幅度变动?测量系统切换?
检验2|连续9点落在中心线同一侧
说明过程发生了稳定方向性偏移,值得高度关注。
排查方向:是否换班、换料?设备维护或工艺切换?
建议覆盖排查区间:异常前后各12组数据,以辨识变化起点。
检验3|连续6点单调递增或递减
表征流程存在缓慢恶化趋势。
排查方向:刀具磨损趋势?操作人员熟练度下降?外部环境(温湿度)波动?设备零点漂移?
⚠️ 此类问题往往不能仅通过图示发现,需结合现场及历史趋势做综合判断。
检验4|14点上下交错波动
反映出数据呈现强烈的交替波动特性。
排查方向:
-
是否由不同产线、班组混合采样?
-
前道工序节拍不稳定?
-
设备是否处于频繁调试状态?
检验5/6|多数点分布在 ±1σ 或 ±2σ 区间同一侧
反映趋势性偏移已开始,但尚未跨越3σ界限。
排查方向:是否为阶段性材料波动?换线?人为调整参数?
检验7|连续15点落在 ±1σ 区间内
波动异常过小,可能存在数据失真或流程固化问题。
排查方向:
-
数据采集存在重复粘贴?
-
测量精度是否不足?
-
是否人为筛选数据、遗漏异常?
-
数据是否混合了改善前后的两个阶段?
检验8|连续8点落于±1σ~±3σ区间、上下交错
代表波动加剧,系统性异常趋于显性化。
排查方向:
-
多班组或不同设备数据混合?
-
上游流程存在大幅偏移?
-
是否存在人为过度干预(调节-反调节-再调节)?

SPC的教材规则并非万能,应根据实际业务逻辑进行灵活调整。
举例:
若某关键尺寸高度依赖刀具磨损状态,磨损后趋小,换刀后偏大,前几件波动显著,则可设计如下自定义规则:
连续5点中,前3点在中心线以下,后2点越过+1σ → 触发报警
该逻辑虽然不在标准规则中,却同样满足“低概率触发”的SPC原则,符合实际业务情境,实用性更强。
核心原则:SPC的应用不是照搬规则,而应结合流程特性,设计适用于本地工艺的小概率判异模型。

SPC的实效性不在于图形美观与否,而在于:
是否能基于控制图中的异常信号,精准定位流程问题并实现提前预警。
-
图异常却不追查 → 流于形式;
-
图异常却查无所获 → 专业能力缺失;
-
图异常能定位问题并完成流程优化 → 真正实现SPC价值。
但这一切的前提是:数据采集策略科学、数据质量可靠。
没有数据策划做支撑,再精妙的分析方法都是纸上谈兵。
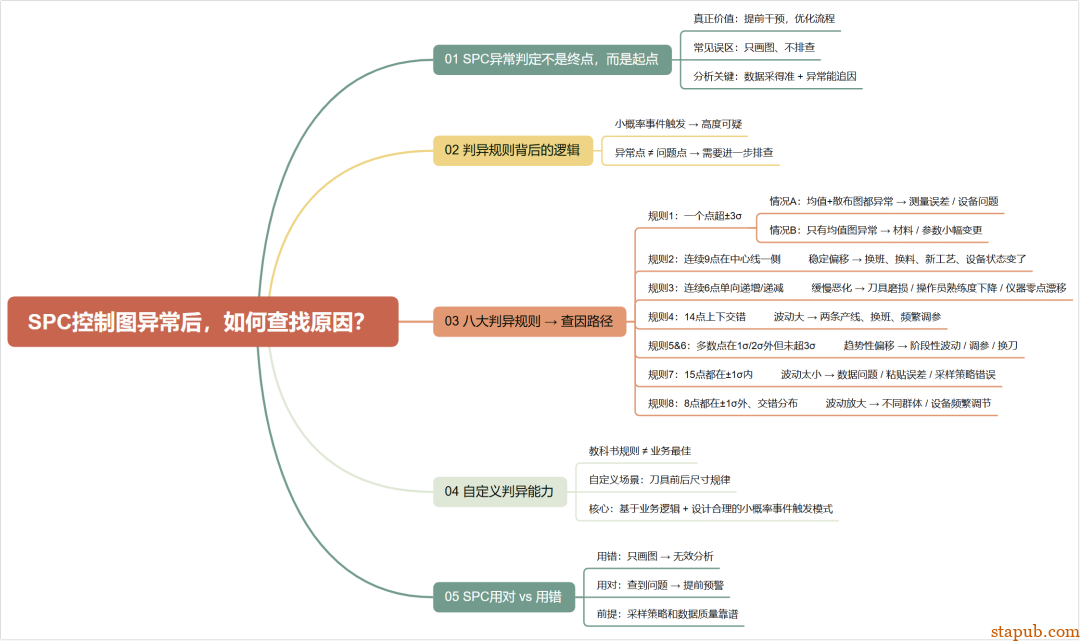
✅ 总结一句话:
SPC不是“画图工具”,而是“流程侦察兵”——图只是起点,排查才是核心,改善才是终点。